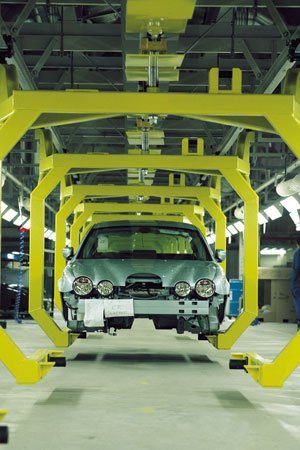
The background to Jaguar provides a good example of entrepreneurship – identifying opportunities, creating a winning formula and responding to consumer needs to build a highly successful company.
The Jaguar story is one of ‘rags to riches’. In 1922, at the age of 20, a young motorcycle enthusiast called Bill Lyons met William Walmsley in Blackpool. Walmsley was building a stylish sidecar to attach to a reconditioned motor cycle.
Bill Lyons saw this as an opportunity to create a winning formula – combining style, elegance and quality, with scale production. He set up the Swallow Sidecar Company, with a bank overdraft of £1,000. In 1927, Herbert Austin introduced his baby car, the famous Austin Seven. Intended to bring motoring to the masses, the tiny Sevens were cheap, easy to drive and reliable but lacked individuality. Here, Lyons recognised another opportunity. He created a stylish two-seater body that was mounted onto the Austin Seven chassis – the new Austin Seven Swallow proved highly popular.
From then on, there was no looking back. With the sales of the cars and sidecars continuing to increase, the company decided to move to the Midlands, traditional heartland of the British motor industry. At the start of the 1930s, Lyons took another bold step – creating a new chassis to Swallow’s designs and arranging for the Standard Motor Company to build the chassis. The SS Coupes were duly presented at the 1931 London Motor show and created a sensation with their extra low bodies and outrageously long bonnets.
In 1935, the ‘Jaguar’ name entered the scene for the first time with a completely new saloon and sports car range. By now the cars had much more powerful engines, new body styles and offered four doors for the first time. It therefore made sense to launch the new model under a new name – hence the birth of the SS Jaguar. After the War, the letters SS were dropped and the Jaguar name went on to gain the prestige and quality with which it is associated today.
Over the years, there have been many different Jaguars – the famous ‘C’, ‘D’ and ‘E’ types, coupes, saloons, four-seater sports cars. In later years, however, they became prestige, luxury cars aimed at the top of the market. Although Jaguar had a fine range of products, the company realised by the end of the 1980s, that it would need the backing of one of the ‘automotive giants’ in order to meet future challenges. In late 1989, after careful research and detailed negotiations, Ford became the new owners of Jaguar Cars. The agreed plans for Jaguar’s future recognised the integrity of the Jaguar marque and stipulated that Jaguar was to retain its strong, individual brand identity.
In the early 1990s, world recession forced Jaguar to engage in a process of reconstruction. The labour force was reduced through planned retirements and voluntary redundancies and the company carried out a process of quality improvement and technical change. By the middle of the 1990s, Jaguar was confident enough to launch a range of new prestige models including the XK8 – Jaguar’s first new sports car for a generation. Early in 1998, Jaguar announced that the mid-sized Jaguar S-Type sports saloon (code named X200), would make its world debut at the Birmingham International Motor Show and that the Jaguar S-Type would be in full production by 1999.
In modern competitive markets it is essential for businesses to be able to innovate. It has been argued that for a large business organisation ‘not to innovate is to die’. Modern production depends on the combination of many factors such as research and development, production engineering, investment in plant and people, as well as the effective use of technology. Few industries have experienced quite as much change in recent years as that of the motor industry.
In focusing on one of the most exciting industrial regeneration projects in this country in recent years, this case study examines how Jaguar has reconstructed a factory at Castle Bromwich in Birmingham to build its new Jaguar S-Type range.
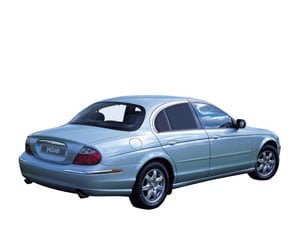
The key strategic reasons for creating the Jaguar S-Type were to:
- extend the Jaguar brand
- generate increased volume (numbers of sales) and hence profits
- respond to the downsizing trend
- appeal to younger buyers
- strengthen the dealer network
- move customers up through the Jaguar range i.e. customers will be encouraged to remain with Jaguar cars, moving from the smaller, more affordable Jaguar S-Type, to the more expensive and sophisticated vehicles.
The Jaguar S-Type competes against the mid/top end of the BMW 5 Series and Mercedes E class.
A new name for a new launch
Jaguar’s classic saloon car heritage provided the inspiration for the name for its new X200 model – the Jaguar S-Type. The original Jaguar S-Type, which went on sale in 1963, combined compact dimensions and sporting characteristics derived from Jaguar’s much-acclaimed Mk2 saloon, with luxury, comfort and a sophisticated mechanical specification.
These qualities perfectly sum up the design philosophy behind the new car. Like the original version, the new Jaguar S-Type combines luxury and comfort with outstanding ride, handling and performance. The styling maintains Jaguar’s long tradition of producing some of the world’s most beautiful, innovative and distinctive saloon car designs.
The target customers for the Jaguar S-Type
Having identified a market segment, targeting takes place. This involves developing a marketing mix aimed at particular groups of individuals. The Jaguar S-Type is targeted at a younger average age of customer than the current XJ Series. There are three distinct target groups:
- professionals in the 30-45 age range (singles and couples)
- executive families in the 40-50 age range (2+ children)
- third agers (couples aged 50+, childless or the children have left home).
Research has shown that the target groups identify certain criteria when buying a car. An ideal new car should be:
- stylish
- fun to drive
- safe
- secure
- high quality
- high performance
- technologically advanced.
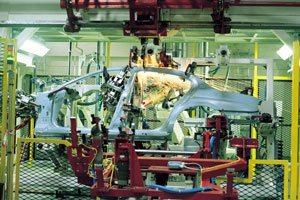
The Castle Bromwich manufacturing facility is certainly one of this country’s most prestigious centres of engineering excellence. The Ministry of Aviation first built the factory in 1938 for Vickers Ltd. From 1939 to 1944, it was used for the production of aircraft – some 300 Lancasters and 12,000 Spitfires. Since then, a range of car parts and other products, such as washing machines, bicycles and radiators have been built at Castle Bromwich.
The role of English Partnerships
English Partnerships was set up to play a major role in the Government’s regeneration and inward investment strategies. Its task is to release the potential of vacant and derelict land in English towns and cities, making the land available for employment, green space, housing or any other use to regenerate the area.
The decision by Ford to invest £400 million in the new Jaguar and the Castle Bromwich plant resulted from clearly thought-out co-operation between English Partnerships, the DTI and the Government Office for the West Midlands. The emphasis was on developing a land regeneration programme that would breathe fresh life into an area which had a wealth of available skills and a proud industrial history.
Statistics for the new development show that the project will:
l create 1210 jobs dedicated to the new model line l create up to 5,000 jobs within supplier companies in the UK
l reclaim 57 acres of derelict land
l service 25 acres of industrial land and provide new community facilities
l ensure Jaguar’s long-term future in the UK and its employment of over 5,000 people
l represent the largest UK inner city investment in the last 50 years.
The plant at Castle Bromwich already had a modern, highly automated body assembly facility for the XJ saloon, together with an advanced paint shop. In addition, there was ample space on the site to establish an additional assembly facility and a new final assembly operation plus the other manufacturing support services. This enabled Jaguar to create an integrated manufacturing centre of excellence for the new car, supported by a dedicated supplier base. Many of the suppliers are committed to establishing new feeder factories in the West Midlands.
The plant
Castle Bromwich is a very impressive facility with world-class plant and processes. Jaguar has completely refurbished three whole blocks in the factory. E-Block is the body construction facility. It was last used in 1986 to produce the Series 111 saloon. The manufacturing in E-Block takes place in a giant U-shape. It follows the logical progression of car manufacture, starting with under-body assembly, followed by body-sides being fitted, welded and validated for alignment, before going on to be fitted with closures – the doors, bonnet and boot – and also the bumpers and front wing assemblies.
The vehicle is washed and inspected before going to the Paint Shop. The painted bodies then enter D-Block on an overhead conveyor system for the trim and final assembly. This involves the fitting of the bumper cover, seat assemblies and instrument panel. The vehicle is glazed and partially trimmed before the fuel tank is fitted.
The assembly then transfers to I-Block where the power-train and front and rear axles are added. The vehicle returns to D-Block for the exhaust, seats, bumper covers, wheels and tyres to be fitted. The electrics are configured and all fluid systems are filled. The wheel and headlamp alignments are checked. Jaguar validates every car’s braking system and power-train on a ‘rolling road’ and confirms resistance to water leaks. The finishing touches are then made to the car on the valet line before passing it on to Sales.
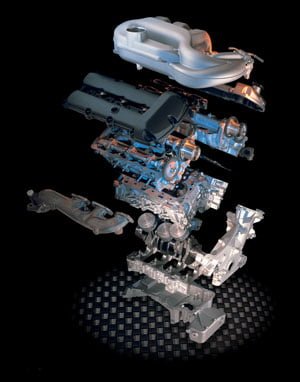
The key manufacturing principle is that robust processes product right-first-time vehicles every time. Right-first-time is a quality principle which specifies that there should be zero defective items. At Castle Bromwich, vehicles have to be 100% correct before they can leave one station and proceed to the next.
To ensure product quality and the most effective processes, the firm operates a process called lean manufacturing. The quality of components is the responsibility of whoever supplies them. This applies to sources within Jaguar as well as to outside suppliers. To maintain tight control over quality, the company operates with minimum stock.
The environmental management programme
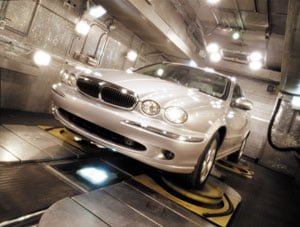
- the regeneration of an old derelict brownfield site rather than using valuable green space
- energy management – a new gas-fired boiler house has replaced the old coal fired one, saving £150,000 per year
- recycling – the new X200 is 85% recyclable by weight
- emission reduction – the new plant has eliminated ozone depleting CFCs and 111 trichloroethane from the manufacturing processes and the product. The new Power House has led to a 95% reduction in sulphur dioxide emissions.
- an environmental management system – Jaguar is committed to the international environmental management system standard (ISO 14001). This standard ensures that processes are in place to identify the impact of corporate activities and formulate measures to improve and, where possible, eliminate harmful or wasteful practices.
- Jaguar and the community – Jaguar is working actively within the local community, participating in and supporting local environmental initiatives such as The Groundwork Trust, Local Agenda 21 and the Coventry Environmental Charter.
Paint process improvements
The painting processes provide a good example of the environmental improvements that have taken place. Traditionally, the majority of pollutants produced in a car plant come from the paint process. Recent environmental legislation has recognised this and requires reduction in overall plant emissions. Jaguar is addressing these issues by a significant programme of investment and material changes.
Old fashioned colour coats contribute 40-50% of solvent vapour emissions. Jaguar has therefore begun using new water-based colour coats (which use water instead of solvent). This has immediately reduced factory emissions. Jaguar has engaged in a £65 million investment in paint shop refurbishment. The key theme is environmental improvements to all processes. Another objective is to reduce energy usage.
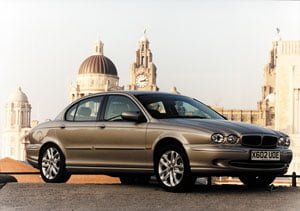
Jaguar continues to evolve – improving manufacturing methods and environmental performance. It is extending its brand with the production of the Jaguar S-Type and is a key player in a major industrial regeneration project. In this way, Jaguar’s winning formula continues.