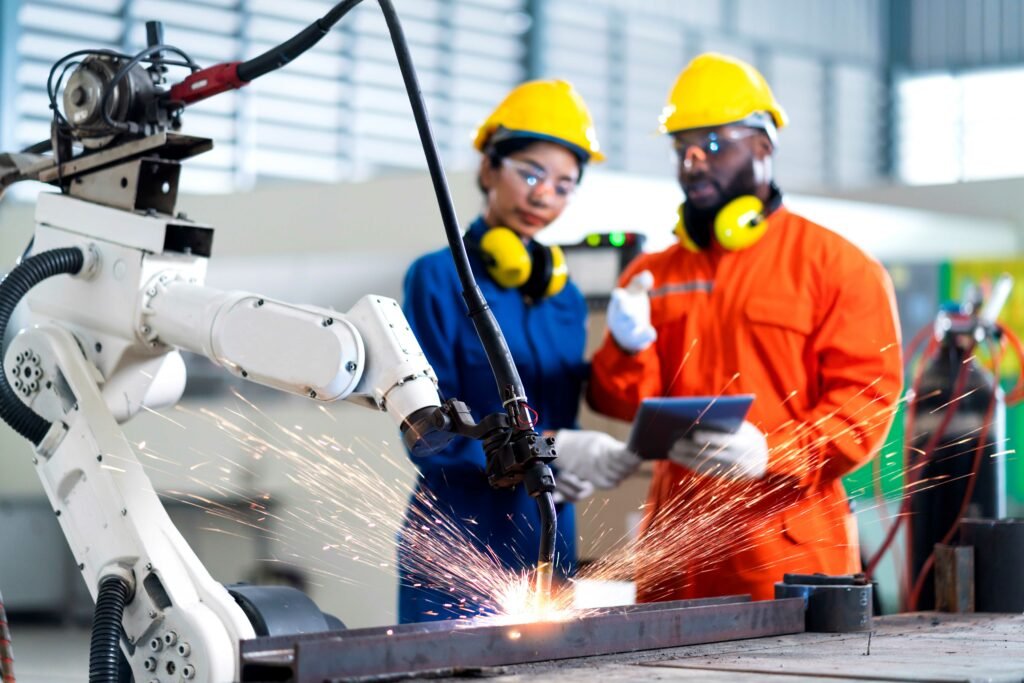
How does Root Cause Analysis Help in a Manufacturing Setting?
Effective root cause analysis plays a pivotal role in diminishing the recurrence of failure components within the manufacturing process. By proactively identifying and addressing the fundamental reasons behind these failures, manufacturers can significantly reduce defects and malfunctions in their products. This benefits both the manufacturing process itself by minimizing disruptions and rework, as well as end consumers who receive higher quality and more dependable products.
There are various powerful root cause analysis tools and techniques for conducting root causes analysis of an incident. Whether it’s a production line issue, equipment malfunction, or quality control problem, for instance, the 5 Whys method can be employed to reveal the root causes behind these challenges, leading to sustainable solutions and process enhancements.
Example: In a manufacturing setting, if a product consistently fails quality checks, using the 5 Whys method may reveal that the issue stems from inadequate training on assembly procedures or subpar raw materials, thus allowing for targeted corrective actions.
Recognizing Issues
Identifying Failure Components
When it comes to the manufacturing industry, dealing with frequent failure components is a significant challenge. These failures can lead to production delays, increased costs, and ultimately affect product quality. Therefore, identifying these failure components is crucial for implementing sustainable solutions.
It is crucial to use root cause analysis software to keep track of these failure components for future references. By pinpointing the specific parts or processes that are prone to failure, manufacturers can take targeted actions to address these issues and prevent their recurrence.
Data Gathering
Efficient data gathering plays a vital role in effective root cause analysis within the manufacturing sector. By collecting accurate and comprehensive data related to production processes, equipment performance, and quality control measures, manufacturers can gain valuable insights into the underlying causes of manufacturing problems. This data serves as the foundation for identifying patterns, trends, and anomalies that can help in uncovering root causes and formulating appropriate corrective actions.
By ensuring thorough data collection and analysis. Manufacturers can proactively address manufacturing challenges and work towards enhancing overall product quality while minimizing the occurrence of failure components.
Analyzing Root Causes
There are various ways to analyzing root causes of an issue. In general, we can divide them into systematic approach and identification of root causes.
Systematic Approach
When it comes to addressing manufacturing problems, taking a systematic approach to root cause analysis is crucial. This involves methodically examining each step of the production process to identify any potential issues that could lead to failure components. By following a structured and organized approach, manufacturers can ensure that no stone is left unturned in uncovering the underlying causes of manufacturing challenges. This systematic method allows for a comprehensive understanding of the entire production system. This will enable the identification of weak points and areas for improvement.
Identifying Root Causes
The cornerstone of effective problem-solving in manufacturing lies in identifying the root of issues. This involves digging deep beyond surface-level symptoms to understand the fundamental reasons behind failure components. By pinpointing these root causes, manufacturers can develop targeted corrective actions that directly address the core issues, leading to long-term solutions rather than temporary fixes. Understanding the underlying factors contributing to manufacturing problems is essential for driving sustainable improvements in product quality and overall operational efficiency.
Collaboration in Action
Team Collaboration
Effective root cause analysis often involves the collaborative efforts of a team. When multiple perspectives and expertise are brought together, it enhances the depth of understanding and insight into complex issues. Each team member can contribute unique observations and experiences. Which can be invaluable in identifying underlying causes that may not be immediately apparent.
Furthermore, team collaboration fosters critical thinking by encouraging individuals to challenge assumptions and consider different angles when addressing problems. By working together, teams can leverage a diverse range of skills and knowledge, leading to more comprehensive problem-solving approaches.
In manufacturing, for example, when addressing a recurring equipment malfunction, involving technicians, engineers, and production staff in the root cause analysis process can yield a holistic view of the issue. This collaborative approach ensures that all relevant factors are considered, leading to more effective solutions.
Effective Communication
Clear communication is fundamental to the success of the 5 Whys Analysis process within a team setting. Open dialogue allows for the exchange of ideas and perspectives, ensuring that everyone’s input is considered. It also facilitates active participation within the team, creating an environment where individuals feel comfortable expressing their thoughts and contributing to the problem-solving process.
To promote effective communication during root cause analysis exercises, it’s essential to encourage open discussions where all team members have an opportunity to voice their insights. Additionally, active listening plays a pivotal role in ensuring that every perspective is acknowledged and integrated into the problem-solving approach.
By fostering an environment of open communication and active participation, teams can maximize the effectiveness of the 5 Whys Analysis in uncovering root causes while nurturing a culture of collaboration and continuous improvement.
Uncovering Root Causes
To uncover root causes, the 5 Whys Analysis proves to be an incredibly effective tool. By delving into the underlying reasons behind issues, this method allows for a comprehensive understanding of the factors contributing to a problem. Its practical applications in real-life scenarios, particularly in manufacturing and other industries, demonstrate its relevance in addressing complex challenges.
The significance of collaboration and critical thinking in the Root Cause Analysis (RCA) process cannot be overstated. Working together as a team fosters a diverse range of perspectives and expertise. Leading to a more thorough examination of underlying causes. This collaborative approach ensures that all relevant factors are considered, ultimately resulting in more effective solutions.
In real-life scenarios, the 5 Whys Analysis can be applied to various situations, such as equipment malfunctions, quality control issues, or process inefficiencies. The iterative questioning approach encourages teams to think critically and dig deep into the fundamental reasons behind an issue. Through open communication and active participation within the team, individuals can voice their insights and contribute to the problem-solving process effectively.
Conclusion
When manufacturers take the time to delve into the underlying issues rather than just addressing surface problems. They open the door to a multitude of benefits. By employing a systematic approach to root cause analysis. They can uncover sustainable solutions that have a lasting impact on product quality and the recurrence of failure components.
- Proactive Approach: Addressing manufacturing challenges through root cause analysis allows for a proactive approach to problem-solving, leading to long-term solutions rather than temporary fixes.
- Enhanced Product Quality: By identifying and addressing the underlying issues, manufacturers can make targeted improvements that directly impact the standards of their products, resulting in enhanced product quality.
- Diminished Recurrence of Failure Components: Effective root cause analysis significantly reduces defects and malfunctions in products, benefiting both the manufacturing process and end consumers by minimizing disruptions and providing higher quality products.
Lastly, it’s worth to note that the effectiveness of Root Cause Analysis lies not only in uncovering root causes. But that said, it also fosters a culture of collaboration and continuous improvement within organizations.