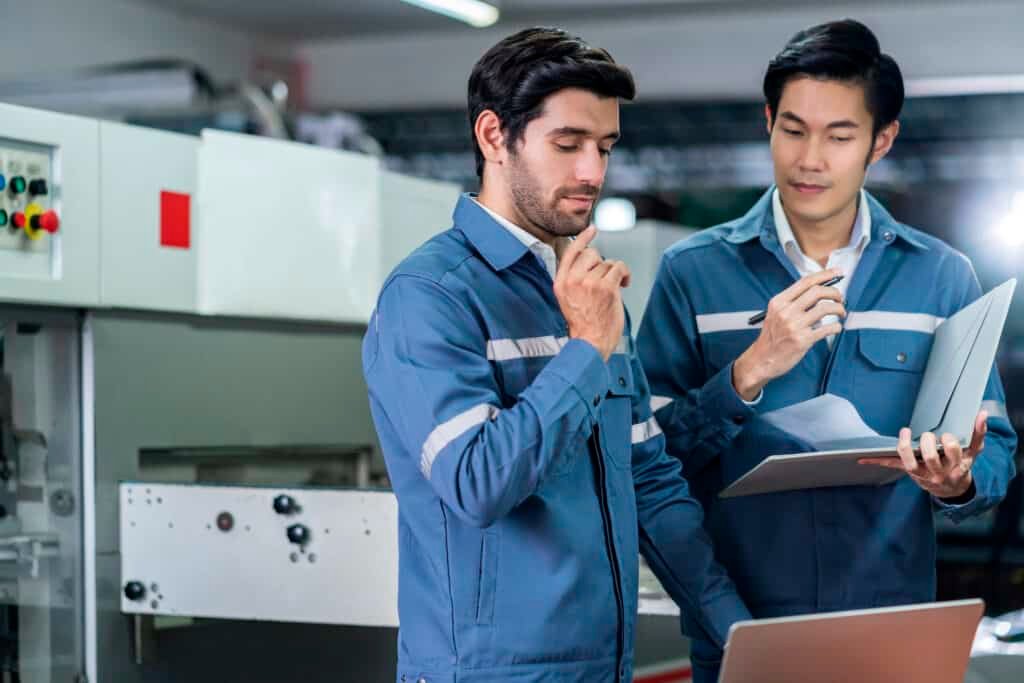
India arguably has one of the largest labour forces in the world, owing to its massive population. With over 500 million, India’s labour force constitutes about 40% of the total population. Industry 4.0 has seen a rise in technologies which aim to improve the quality of work. This will create an upskilled labour force, with the introduction of human-robot collaboration, automation of knowledge work and digital performance management. As part of one of the largest economies in the world. Indian manufacturers now need to focus on keeping up with new advancements that are catapulting other economies to the top. This article will take a look at how important the Indian manufacturing landscape is, and what India can do to become one of the leading manufacturing hubs globally.
India as a Global Manufacturing Hub
With the technological and digital advancements that the current Industry 4.0 has brought. India has slowly emerged as one of the global manufacturing hubs. India’s manufacturing sector contributes to nearly 16% of the country’s GDP, and the Government of India has a target of increasing this contribution to 25% by 2025. Which gives it an estimated US$ 1 trillion and creates about 100 million more valuable jobs in the process. Various global industry leaders are now seeing the benefit of investing in factories and workforces in previously unexplored geographical areas. Thus, there has been a steady increase in the number of foreign investments in the Indian region over the last few years. This fast-paced growth in the number of large manufacturing plants and factories directly results in an immense increase in the number of jobs created. The scope for India to become an even bigger globally recognized hub has also increased due to the onset. The repercussions of the COVID-19 pandemic. As the world sees industrial crashes in some of the world’s largest manufacturing points. New opportunities can arise for Indian manufacturers to take over the role of the world’s leading manufacturing hub.
The Path to a Self-Reliant Nation
To utilize the vast opportunities that have risen during Industry 4.0 to their maximum potential. The Government of India has proposed many ambitious schemes to convert India’s manufacturing sector into an even more prominent global hub. The most notable of which is Make in India. Initiatives like Digital India, Start-up India and Skill India all aim to cultivate and nurture the diverse and potential talent that India’s workforce harnesses. The nation to an even more impressive global economic position. The initiative has succeeded in creating more valuable jobs, expanding the GDP and creating an overall development of rural and urban India. There still exists a larger scope for the movement.
The vision for India to become a self-reliant nation, or “Atmanirbhar Bharat” is modelled on the basic building blocks that India as a nation needs to step into a larger picture and push itself to a much higher position in the global economy. Once India transforms into a “self-generating” nation it nurtures the potential of diversity in talent and skill. There will emerge more value-driven markets which are stable in nature. The Atmanirbhar Bharat vision has indeed given rise to various funding and incentives to manufacturers leading to greater technological advancements, spanning from the growth of personal protective equipment to advancements in digital communication with the emergence of our own 5G network. While these have paved the way for a more self-reliant India. The manufacturing sector still needs higher-valued incentives and support to reach global standards. In order to do this, however, India must start investing more in Industry 4.0 solutions that provide quick and safe alternatives to the current manual processes.
Investing in Technology Human-Robot Collaboration
One smart solution that has emerged in Industry 4.0 is a human-robot collaboration or HRC. HRC is built on the concept that a human and a robot work together in the same workspace. This is by performing tasks in a collaborative manner. In a country like India where there is a massive influx of labour. It is important to make sure that jobs are not lost under the pretence of development. Humans and robots working in a collaborative manner can be a very useful solution to this. This will allow a robot to act as an assistant to employees, thus performing dangerous. And repetitive tasks which were previously done by humans. And relieving them of ergonomic and other health-related risks. In this way, new technologies will not replace the human workforce with robots but instead will create an environment. Where human employees and robots can share skills with each other. With the assistance of a robot, employees can now utilize their time harnessing the skills that they possess. Learn new high-valued ones, while “teaching” the robot their own skills. So that the robot can perform the tasks with more precision and speed.
Collaborative robots or cobots are built on this very concept of HRC. Cobots are complex machines that work hand in hand with human operators. This lightweight and flexible technology is slowly reinventing industrial robotics. The manufacturing landscape, as it can be utilised to automate a variety of tasks while allowing humans to work alongside it in a safe environment without posing any health-related risks. Unlike traditional robots, cobots do not require any protective fencing around them (subject to application risk assessment) as they are equipped to work with safety measures. This allows humans to continue their daily work without any hindrance. Thus, cobots do not act as a replacement for humans but instead, as automated assistants. This will allow humans to continue their work with more ease.
Cobots can be used to automate a large variety of tasks to boost the Indian manufacturing sector. From assembly line processes such as screw driving to end-of-the-line applications like packaging. This niche technology has proven to be quite resourceful for manufacturers who are looking to optimize their production. In fact, cobots can be used to automate almost all industrial processes pick and place, screw driving, moulding, packaging & palletizing, machine tending, welding, quality inspection, and even lab analysis. Their small footprint, low energy consumption and easy programming make them exceptionally useful for both large-scale and small-scale industries. Re-assignment of repetitive and physically taxing tasks to cobots also results in people being employed for more value-added strategic work such as operating the cobots. This will create more jobs that add value to firms.
Collaborative Future
India has a large network of SMEs and MSMEs which play a pivotal role in India’s global economy. It is important for these industries to adapt to the various Industry 4.0 solutions. Methods in order to maintain steady growth not only at home but even globally. Many of these industries have already invested in smart HRC solutions. This will enable them to not only grow production levels and customer satisfaction but even upskill and nurture their employees. Cobots in particular have proven to be a very convenient solution for these firms. They no longer need to sacrifice any shop floor or human talent to deploy robotic technology. In this way, HRC has already played a notable role in supporting the growth of SMEs and MSMEs and providing them with valid incentives for them to continue investing in the long term.
Cobots are one of the fastest-growing technologies in the industrial automation space today. The current statistics show that the cobot market is set to grow at about 45-50% CAGR. Which is by far the fastest-growing segment in industrial automation. In India however, many manufacturers view this as more of a cost rather than a long-term investment. With the right incentives, manufacturing firms will be able to shift this thought and start looking at it as an investment. This will help them achieve global standards of quality for their products.
To become a global manufacturing hub, Indian manufacturers must start switching to solutions. Such as HRC to improve production efficiency, quality and workplace safety. Engaging in new technologies will enable manufacturers to monitor their processes from start to finish. While making sure that the customer’s satisfactory quality levels are met. Manufacturers will be able to work around the clock without worrying about the safety of their employees. By investing in technological solutions which are not labour-dependent, industries will even have protective armour against any future crisis such as the ongoing COVID-19 pandemic. Labour will automatically be upskilled and a balance between the technology and the employee teaching each other will be created. Investing in such new technologies will optimize production levels and cost-effectiveness. It will help in the emergence of more valuable jobs, creating a more efficient and value-driven market. Which will help put India at the centre stage of technological manufacturing hubs.