
Some business improvements involve a giant leap forward. An example of this would be the development of a revolutionary new product such as the bicycle or, more recently, the iPod or modern wind turbines to create green energy. However, of more importance to most businesses is ongoing small step improvement. This case study shows how Leyland Trucks continually makes improvements to everything it does based on the Japanese principle of Kaizen.
Background to Leyland Trucks
Leyland Trucks manufactures trucks under the DAF brand in Leyland near Preston, Lancashire. As well as production in the UK, DAF manufactures in Eindhoven in Netherlands and Westerlo in Belgium. Leyland and DAF are both part of the North American company, PACCAR Inc.
In 2006 DAF’s three manufacturing plants in Europe, including that at Leyland, produced a record 56,700 trucks of between 7.5 and 44 tonnes (the heaviest vehicles on the road). One in every four trucks sold in the UK is by DAF. New truck registrations in Europe were almost 268,000 in 2006 and DAF currently has a 15% share of this European market.
Business strategy

The current business objective is to increase the market share to 20%. When a company wants to achieve its objective, it needs to have a plan to get there this is termed the strategy.
DAF’s strategy for Leyland to achieve this objective has two main elements:
- continuous improvement
- increasing production capacity from 18,000 to 25,000 units.
Continuous improvement, or Kaizen

The Japanese term ‘Kaizen’ means continuous improvement. It comes from the words ‘kai’ continuous and ‘zen’ good or for the better. We
use the term ‘Kaizen event’ for any action that is an improvement to an existing process.
‘Kaizen’ means continuous improvement.
Kaizen events usually involve bringing together operators, managers and the owners of a particular event to discuss possible improvements. A flowchart illustrates the process and people discuss how they can improve the flow of work. Lots of small steps can rapidly become a giant leap forward in the creation of new ideas. The great thing about the Kaizen process is that people who really understand manufacturing at a nuts-and-bolts level can get involved in introducing improvements. Someone who assembles part of the truck suspension will have a reasonably good idea about how the processes they work on could be improved. Leyland therefore encourages everyone to be involved in decision making.
How Kaizen works

A good example of how Kaizen is implemented at Leyland relates to the introduction of a robotic paint spray booth for the truck chassis. This was a huge leap forward Leyland was the first assembly plant in the world to use robots on a moving conveyor to paint its chassis. It planned to implement this over the summer shutdown of the plant this is where Kaizen came in. One of the first steps was to look at the successful introduction of a production line the previous year. The purpose of this was to identify all the lessons that could be learned from the earlier project and to apply them to the new chassis spray booth. Everyone was able to put forward their views and all appropriate ideas for improvement were considered.
Why use Kaizen?
There are a number of major reasons why Leyland Trucks practises continuous improvement:
- to meet the production and sales growth plans
- to meet customer demands for more reliable trucks
- to stay ahead of the competition. For example, there is always a risk that rival manufacturers, e.g. in China and other European countries, might merge (this happens when two companies join together). This could lead to a threat from these bigger competitors
- to offset rising labour costs. Wage costs rise every year. Leyland is not able to raise prices because of competition, so any increase in wages has to be compensated for by more efficient production
- to protect jobs in the UK. If operations at Leyland Trucks were considered inefficient, there would be a danger that senior managers at global headquarters might want to move production to a location with lower wages.
Setting and monitoring continuous improvement goals
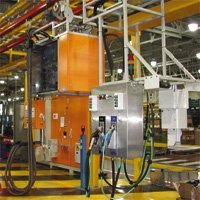
Businesses seek to ‘measure what is measurable’. These measures are usually set out in what are referred to as Key Performance Indicators (KPIs). In order to check on the success of continuous improvement, it is important to have a number of measures in place. In this way, the company can see where improvements have been made. In order to check on the success of continuous improvement, it is important to have a number of measures in place.
The measures that Leyland Trucks uses are clustered into a number of themes these are areas of business results that are similar. For example, one theme is Health and Safety. Useful measures under this theme are the number of accidents at work, and illness-related issues.
KPIs
The main themes used are:
- on-time performance (meeting deadlines)
- productivity (how much is produced from given resources in a certain time period)
- quality (for example, the numbers of defects ideally zero)
- financial (for example, costs)
- inventory (the quantity of stock held)
- health and safety (reportable accidents, minor accidents)
- continuous improvement (Six Sigmasee below).

One or more KPIs are used to measure each of these themes. For example, the measure of productivity calculates the number of labour hours required to manufacture each truck (known as ‘truck hours’). All of this information is set out on a chart, which is monitored each week. In the chart, you can see examples of productivity-related KPIs for a week at the end of 2006.
In the first measure of this fictional example, the goal for truck hours for 2006 is 52. For the year to date, results are above the annual target. In the second, you can see that in 2005 each employee produced an average of 14.9 trucks per week. The goal for 2006 was to raise this to 15.6. For the year to date, the average truck production numbers are on target.
Six Sigma
An important KPI for continuous improvement is Six Sigma. This is a measure of quality that strives for near-perfection. To achieve Six Sigma, a process must produce no more than 3.4 defects per million opportunities. Six Sigma uses statistical tools and data as a base for analysis. It can be used to improve existing processes or develop new ones. It involves the systematic identification of defects and deficiencies within any product, system or process, with a view to eliminating them. A defect is anything that is outside customers’ expectations. With its disciplined and logical approach, Six Sigma enables decision-takers in Leyland Trucks to improve their understanding of business and operational processes. This results in major cost savings and the development of best practices.
Visionary targets
Leyland Trucks sets targets to create a vision for staff to work towards. In other words, it gives a clear picture of what can be achieved through high performance. In 2001, the Managing Director (MD) of Leyland set a visionary target for quality in the company based on a Quality Index. Quality relates to such areas as the number of breakdowns within 90 days and mechanical defects.
Leyland Trucks sets targets to create a vision for staff to work towards. In 2001 the value of this index was running at 13.2. In order to drive a reduction in these breakdowns and defects, the MD set the visionary target of 5.0. Leyland has achieved this target. Progress is benchmarked across PACCAR’s nine manufacturing plants. Leyland is well ahead of its ‘sister’ plants.
A culture for continuous improvement

It is usually quite easy to get a feel for the culture of a company. For example, does the business look after customers? The culture at Leyland Trucks is based on trust. It involves everyone in the continuous improvement process. The company’s culture relies on a set of values. A value is something that an organisation and its people believe in. Values determine the way we behave.
Leyland’s values support continuous improvement and include:
- training for everyone for example, identifying ways in which people can contribute to continuous improvement such as by eliminating errors and waste
- team-building for Kaizen
- involving everyone from top to bottom in decision-making
- empowerment giving responsibility and power to everyone in the organisation, encouraging them to make decisions and to take on responsibility for continuous improvement
- innovation encouraging everyone to be prepared to think of, communicate and try out new ideas.
Living the values
These values are translated into practical action this is referred to as ‘living the values’. They are put into practice through:
- day-to-day sharing of ideas between team members
- weekly briefings where team leaders inform members of new developments, issues, problems and successes
- quarterly newsletters for all employees
- teamwork sessions
- celebrating achievement of individuals and teams every three months
- whole-team sessions led by the managing director every six months.
Continuous improvement in action
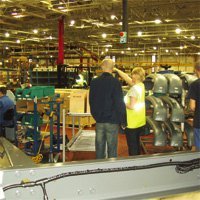
Leyland Trucks has clear targets for continuous improvement and clear processes for building teams and encouraging involvement. Kaizen describes all those processes that involve Leyland’s people in day-to-day small step improvement. ‘The culture at Leyland in terms of the pride that the employees take in being the best is unique. A good example of this process occurred in May 2006 at the vehicle finishing part of the plant. This involved a High Impact Kaizen Event (HIKE) where six pairs of project leaders were chosen to work with employees in this area. Each member of the HIKE team wore a brightly coloured ‘high visibility jacket’ and they examined every area of work, talking to everyone on the section in an informal but systematic way. They encouraged everyone to identify workbased problems and possible solutions. Staff got together at working lunches to discuss work issues. Overall, the idea was to involve everyone so there would be no surprises. A senior manager was also on hand to work as a coach, helping and supporting the HIKE team.
The HIKE was an outstanding success because of the improvement culture at Leyland. At the end of the project the team leader stated that ‘the culture at Leyland in terms of the pride that the employees take in being the best is unique. You only have to spend a week at Leyland to see why they are number one: the employees.‘ More than 200 ideas for improvement were suggested by ground-level employees. The changes they suggested led to:
- a reduction in truck hours of over 17%
- 20% reduction in line-side materials (inventories)
- 23% reduction in walking (the distance that employees had to cover to carry out their work 57 miles per day in total).
At Leyland, over 10% of the 1,000 workforce consists of qualified continuous improvement practitioners. These people run and monitor progress through Six Sigma.
Conclusion

Continuous improvement helps a business to keep ahead.
It is a process that involves all employees within an organisation and is based on a culture of trust and empowerment. The results for Leyland Trucks in its full range of KPIs have been staggering.
For example, in 2006, there have been:
- muliti-million pound savings resulting from Six Sigma
- a rise in on-time delivery to over 95%
- 10% reduction in mechanical defects per unit
- 45% reduction in reportable injuries and 10% in minor injuries in the same period.
The important thing to remember about continuous improvement is that, as the process improves, the targets in the KPIs will also advance. This delivers an ongoing cycle of improvement.