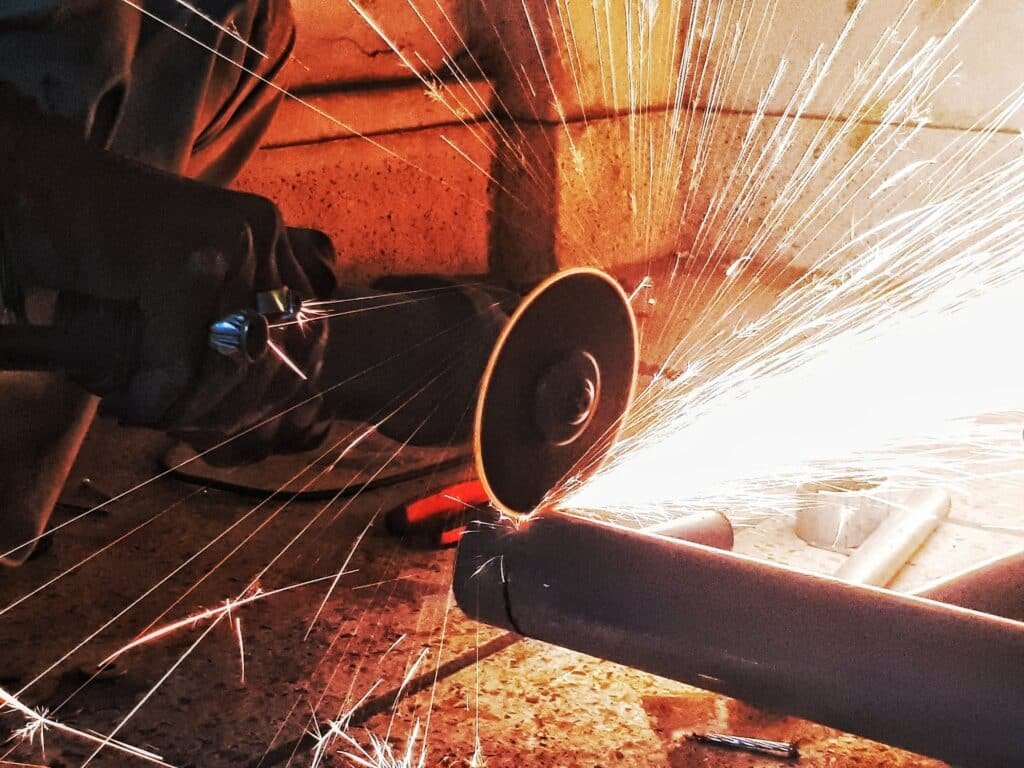
Stainless steel has a wide range of applications in the industrial and consumer industries due to its excellent appealing looks, high strength, and corrosion resistance. The Steel casting tech comes with many advantages, including lower manufacturing costs, increased energy efficiency and improved environmental quality. Because of these advantages, stainless steel is used to make mining machinery, combustion engines, steel pipes, valves, and other equipment that rely on steel casting in manufacturing other products. Another advantage in the steel casting industry is reducing scrap steel utilized in steel recycling as a low-cost source of raw materials, significantly reducing scrap metal.
An ongoing metal casting research offers discoveries and advancements in the casting process, such as the advent of lost foam casting and computer-based visualization tools for die casters to build alternative molding techniques. These sophisticated casting technologies enable foundry researchers to produce defect-free castings while also investigating the details of new casting process parameters. Furthermore, due to deteriorating environmental conditions, businesses have developed simulation-based castings to reduce waste and operational costs. Here are several developments in the steel casting industry;
The Lost Foam in the Steel Casting Industry
Lost foam casting is a process of creating intricate metal components and parts in which molten metal evaporates through a foam mold that is maintained constant by sand. The procedure begins with a polystyrene foam mold, which can be machined from a foam block, carved, or manufactured by an injection molding process.
For the first time in the steel casting industry, the foam design was used in 1958. Although not as prevalent as sand mold casting or permanent casting, this mold casting method offers some benefits, especially when manufacturing complex and precise molds. Unlike traditional techniques, which need expertise in the pattern removal phase and include the pattern withdrawal procedure before casting, the pattern is evaporated when the molten metal is introduced into the lost foam method, eliminating these concerns.
How Is a Lost Foam Pattern Made in Steel Casting Industry?
The pattern can be physically cut or machined from a solid foam block; if the geometry is simple enough, it can be made via a hot-wire foam cutter. If the volume is large enough, the design can be mass-produced using a process similar to injection molding. Following that, steam is applied to the polystyrene, causing it to expand even further to fill the die. The ultimate design comprises 97.5 percent air and 2.5 percent polystyrene. You can hot glue pre-made pouring basins and risers to the template to finish it.
Casting Process in the Steel Casting Industry
The design is then painted with insulating paint, placed in a flask, and surrounded by unbonded sand before being compressed. The covering paint increases the mold’s longevity, protects it from erosion, and prevents breaking. On the other hand, the flask is built for this approach so that when the molten metal is put into the mold, the gas produced by foam burning is evacuated. The foam design is burnt off, and the casting is made after molten metal is put into it.
What Are the Advantages of the Lost Foam Casting in Steel Casting Industry?
1. lost foam casting e creation of complicated castings.
2. It guarantees high precision and a smooth surface finish.
3. This casting guarantees almost no errors or defects.
4. Because it uses only a few processes, this approach is often less expensive than investment casting. Foundries may save a lot of money on labor and production by using the lost foam method.
Application of Lost Foam Casting in the Steel Casting Industry
This technology is frequently preferred to develop sophisticated and elaborate items because of its accurate casting ability. It is used in various fields, including civil engineering, agriculture, national security, automotive, and computer technology.
The lost foam casting method is ideal for a wide range of cast goods, including pipe fittings, pipe fittings, valves, cylinder blocks, fire hydrants, motor starters, 3D models, gearbox details, and more.
Lost foam casting is also used to create highly intricate and complicated lamp posts, gas burners, fences, pump housing, aluminum castings, pan supports, and other items.
Simulation Technologies in the Steel Casting Industry
In the past, goods and services had to be sacrificed for the sake of experimenting. The simulation of the casting process sparked an industrial revolution in the steel casting industry. Engineers predict the outcome of their steel castings before the molds are produced. The program captures the entire casting process, from the design table to tool engineering and foundry operations, and estimates how the casting will perform in the field. Casting simulation software replicates how engineers decide about casting virtually and evaluates each choice to identify design changes that might improve casting quality while simultaneously reducing production costs, tooling, and lead time.
The casting simulation software strives to simulate physical phenomena such as stainless steel solidification patterns, mold filling, and casting phase shift. For them to recreate these events in a computer program, they require a set of governing equations. These modeling approaches have advanced to the point that they can accurately predict castings’ microstructure and mechanical characteristics. They can also detect internal flaws like sand inclusions, shrinkage porosity, and cold. These simulation programs are used to generate new castings or standardize existing castings for any design changes to increase yield without testing them on the factory floor. As a result, casting simulation is becoming a must-have technology in modern stainless steel foundries. No foundry can produce high-quality castings, particularly integrated castings, without simulation for the first time.
Application of Casting Simulation Software in the Steel Casting Industry
Method Optimization
Solidification simulation is crucial for achieving the best possible casting quality. Simulation software saves time and money by decreasing the quantity of shop-floor testing for both new and existing castings in the steel casting industry.
Design Improvement
A thick junction and an extended thin portion in a casting might generate cold shut and shrinkage porosity. If a component designer finds himself in this situation, he should immediately hire a foundry professional to analyze the part’s castability using casting simulation software.
Casting Troubleshooting
Simulation software may troubleshoot a current casting issue, such as a high or variable internal flaw, such as cold shuts and sand. It can also help to improve casting yield.