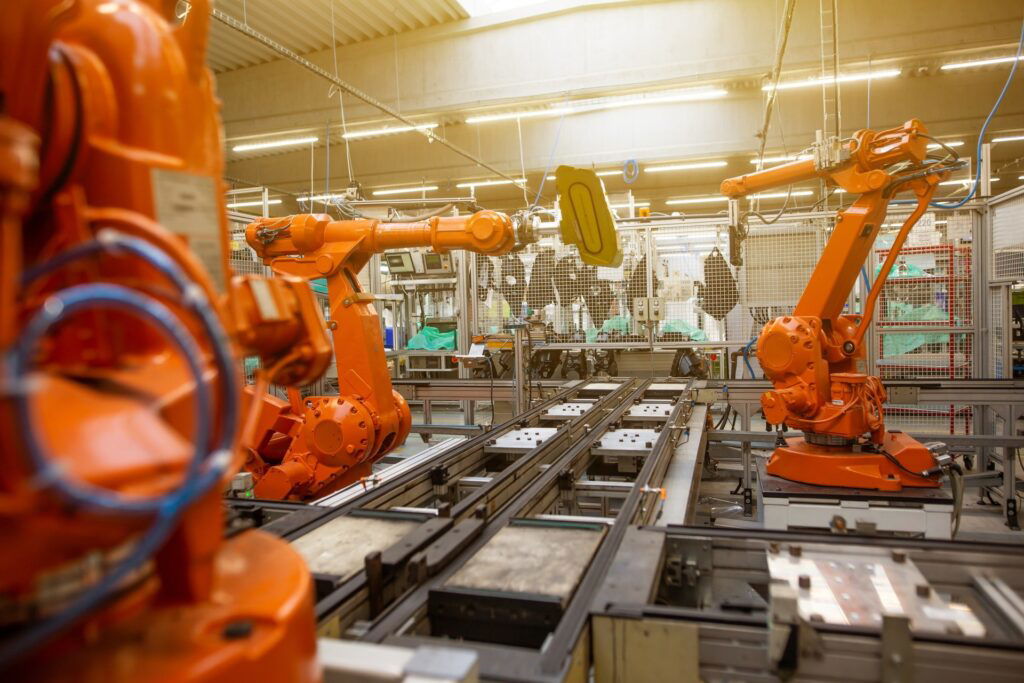
Manufacturing parts have gone through a lot of changes, over the last decade. Today, most manufacturers use additive manufacturing over the old methods that required the subtraction of material, instead. One of the most popular processes of the new method is called PBF, which stands for Powder Bed Fusion. Here is more about these revolutionary 3D printing machines, that have invaded the market.
What is a PBF Additive Manufacturing Machine?
A powder bed fusion machine, such as Formup, uses different technologies, all inside one. In order to function, it needs raw material, which is usually made up of plastic or metal and sand. In order to transform this material into a new object, it utilizes a strong source of energy, such as a laser (most of the time). There is a build platform inside it, on which the product will be put up, layer by layer, as the coater spreads a new sheet of powder material, every time the previous one has been fused together with the main object.
What are the steps to produce a New Object?
The production process takes place according to the information that is transferred to the machine, via CAD software. Engineers create the design inside that software, and the plan is then transmitted to the PBF, which then proceeds to the creation of the part. It is a 3D file, that needs to be exported into a 2D layer format, such as an STL file.
When the process begins, there is already one layer of material placed on the platform. The machine will start by fusing the first layer available. Once that is completed, the build platform will drop one notch, before positioning a new coat of material for the machine to work with. That is how it is able to create the object, one layer at a time, by fusing each of them together, a new one over the last.
The final step is called post-processing. It consists of removing the dust of the unused powder that is left behind, once the final product is completed. The machine does that itself, by cleaning the part. To make sure that nothing is left behind, it often uses a bead blasting system to shake off any dust that may have remained on the object itself. This technique also helps to smooth the surface of the part. Afterwards, if required, polishing can be applied to make it shine, or a dyeing process can also occur if it needs to be coloured. There are other coatings available, which include solvent vapour smoothing, painting and electroless plating, amongst others.
Advantages of PBF Additive Manufacturing
PBF machines are recognised as one of the processes that create the strongest objects. For those who know about isotropic properties, let us mention that the parts created with them are strong in the X, Y and Z (height) directions. Naturally, compared to the previous manufacturing methods, this one takes a lot less time to complete and saves a lot of money for both the manufacturer and its customers.