
When we think about the cost of an aircraft, we tend to think of the cost of buying the product rather than the costs of running it! British Aerospace’s service to the customer does not stop at the aircraft acquisition stage when the aeroplane is sold to the customer. If anything, this is when the customer relationship begins.
This case study focuses upon the processes involved in costing aircraft components. Given the high specifications to which designers have to work, it is important to develop a price for customers which provides ‘Customer Satisfaction at Competitive Cost.’ British Aerospace is a major player in the world aviation industry. Its Military Aircraft Division aims ‘to remain number one in Europe and World Leader in the Military Aircraft Business.’
The design challenge
The challenge to design teams is to design an aircraft that achieves maximum mission effectiveness at minimum cost to the customer. Typically, a military aircraft has a service life of over 30 years. The total operation and support costs such as those involved in owning and operating an aircraft (spares, repairs and servicing) over this time, outweigh the initial cost of acquisition. Therefore, total Life Cycle Cost (LCC) must be minimised in the customer’s interest. The study of the cost of acquisition, operation and support and disposal is known as Life Cycle Cost analysis. To achieve the design challenge, British Aerospace use two main cost reduction techniques.
Re-Engineering
Re-Engineering to reduce the business cost base Since 70% of the final product consists of vendor/bought out equipment, British Aerospace’s suppliers’ performance is critical to enable British Aerospace to achieve improvement, obtain better customer satisfaction and win more business in this competitive environment. Within the Military Aircraft Division, British Aerospace has introduced a Preferred Supplier Process which is designed to improve the performance of the supplier base in meeting the wider aims of the business. There are three elements against which a supplier’s business is assessed:
- Statistical process control;
- Detailed business assessment;
- Measurement of performance.
Multi-functional teams are examining the ways in which these companies operate to ensure that these compliment British Aerospace’s internal business process re-engineering (BPR) in the production of a ‘world class’ best practice.
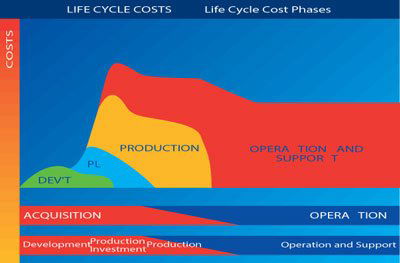
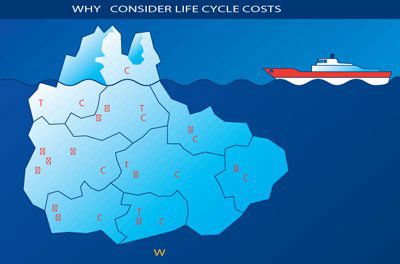
During the design stage, the earlier the opportunity for improvement can be identified, the less it will cost to incorporate. Initially the benefits exceed the associated cost of investment, resulting in a reduction in the life cycle cost. However, there is a point beyond which increased investment will not yield greater savings and the life cycle cost cannot be reduced further.
Life cycle cost analysis is the technique of predicting future costs early enough to enable decisions to be taken that influence design to minimise lifecycle costs without compromising the performance of an aircraft.
Production costs
In considering the life cycle cost elements of a project, which relate to the costs of design, development, manufacture, operation and support of the aircraft, this study now focuses on the manufacturing element of the life cycle cost with particular reference to the ‘in-house’ production manufacture cost.
This part of the life cycle cost, the in-house production cost, accrues all the costs related to turning the concept and design into an actual flying aircraft, capable of performing to its desired requirements.
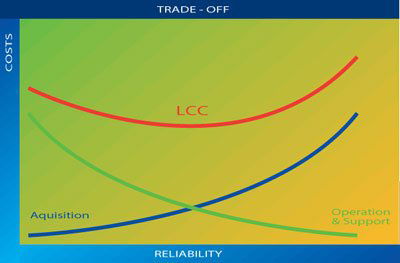
Having highlighted earlier the importance of the utmost reliability and ease of maintenance, it can be seen that it is essential for components to be designed and manufactured with this in mind, whilst ensuring the need for accuracy in productability, quality and affordability.
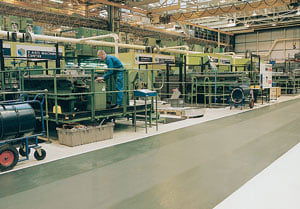
It is important to understand the overall process from receipt of the request for price to the delivery of a product to a Customer. Within this case study, we will focus on the manufacturing cycle and the associated costs for the manufacture and supply of Wing Rib Assembly kits.
The first stage is developing the manufacturing process, associated tooling methodologies and identifying raw material requirements for all components within the assembly. There are two elements to consider:
- Non recurring costs;
- Recurring costs.
Non recurring costs refer to the start up costs and usually include items such as the design and the manufacture of specialist tooling which is a one-off cost prior to commencement of the component production manufacturing phase
The recurring element refers to the specific component manufacture costs and relates to the quantity per aircraft set. Production engineering break out the individual parts of the wing track assembly and plan the sequence of events and operations to convert the raw material into the finished components. A planning document holds various information specific to the part. This ensures that the format is consistent across all the parts. Its prime responsibility is to provide an accurate best practice method of manufacture for all processes. Best practice refers to the optimum method of manufacture to ensure British Aerospace retains its competitive edge in the marketplace.
Recurring costs within the manufacturing process
Raw material is purchased in a configuration suitable for loading on to the PRIME machine – Automax III The billet condition of supply has been established via a ‘Make’ or ‘Buy’ exercise. The relatively ‘low value’ processes of shaping, drilling and tapping has been proved most cost-effective when performed by the material supplier.
Material costs are a fairly straightforward. The major cost driver within the assembly is the Aluminium Rib which constitutes 80% of the total material cost. In this case, aluminium billet is a relatively routine purchase. Values have to be agreed with the supplier covering the drilling and tapping of holes in conjunction with the surfacing and shaping of the billet. This will result in increased costs being agreed for work over and above the raw material costs, which are calculated on current market prices of £s per kg.
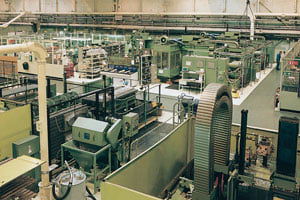
The measurement system used to generate these man-hours is based on the development of synthetics. Synthetics are tables and formulae derived from the analysis of accumulated work measurement data, arranged in a form suitable for building up standard time, machine processing times etc. by syntheses. Syntheses are a technique for establishing the time for a job, at a defined level of performance by totalling individual element times. These element times being obtained from time studies on other similar jobs. Pre-determined motion time system (PMTS) is a work measurement technique whereby times are established for a job at a defined level of performance. The advantage of such a system is the consistency of the output irrespective of the aircraft project being measured.
Man-hour estimates are derived and presented in terms of run and set-up times providing the basic values. Set time relates to a one off cost associated with the manufacture of a quantity of the same component known as the batch size. For example, the prime machine used for the manufacture of the Wing Rib will require the tooling specific to that part and the tooling carousel loaded with the cutters prior to the loading of the first component billet.
The batch size is linked to the customer delivery programme. The availability of the facility is balanced against other projects, but the batch should be of a size that is cost efficient. The run time relates to the repetitive activity performed for each component in the batch.
Converting data into a Cost
Performance is effectively the variance between the measured theoretical time and recorded actuals. The decision to apply performance and at what level, depends upon the activity being undertaken. For example, an automated process is far more likely to achieve 100% of the theoretical target, than a labour intensive process. Therefore, the manufacturing process and the component design are critical to the performance decision making process considerations.
The standard time man-hour value represents the application of techniques designed to establish time for a qualified worker to carry out a specified job at a defined level of performance. The motivated operator would be familiar with the task being performed and have all the necessary tools, equipment and components readily available at the work station. Whilst the application of a performance to standard times can bring reality to the value for some of the above criteria, another allowance has to be added to account for learning. This is done by application of learning curves.
These are widely used in industries where the typical number of units manufactured in a products life cycle is between 5 and 1000; typically shipbuilding, special electronic equipment and of course the aerospace industry. It is difficult to decide whether learning curves are invented or discovered. In the 1930s, philosophers investigating how people learnt, conducted laboratory experiments which recorded how the length of time to complete a task reduced with the number of repetitions of that task. They noticed a mathematical relationship between the results and without going into the maths, the time taken reduced by a fixed percentage every time the total number of repetitions doubled.
Generally speaking, in the aircraft industry, learning curves are in the range of 75% to 95%. The value of the curve varies depending on a number of factors including:
- build rate at which units are made;
- level of skill required to perform tasks;
- organisational experience in managing this type of work;
- level of automation involved;
- levels of planned investment to update production equipment with new technologies;
- standard of special tooling/jigging and fixturing.
We have now established within the costing process:
- material costs;
- man-hours/performance;
- a learning curve.
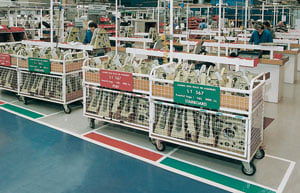
Excessive variation due to changing process elements such as tool wear are detected by the control charts and the process parameters are then adjusted accordingly before the statistical process limits are exceeded and scrap produced. These percentage values applied to future work is likely to be lower than past historical data and these improvements in working practices help to create a competitive advantage over British Aerospace’s competitors.
Support costs – These relate to the various supporting departments within any organisation including Project Management, Production Engineering and Technical Departments which are involved in the project and whose contribution must be included in a price. A charging rate is provided by the Finance Department. This rate is comprised of all the other cost to the company, such as the building, electricity and depreciation. The format of this charging rate varies between companies and will be dependant upon the methods used to allocate cost.
Converting data into a selling price – These processes are key activities which ultimately provides man hours and material costs to the Commercial organisation who are responsible for converting the basic data into a selling price. Should the company be successful with the bid, then the basic man hours and material costs will form the basis of the manufacturing budget against which performance will be regularly monitored. Adverse performance is highlighted and corrective action taken to ensure the appropriate level of return on the business is delivered.
Responding to the request for price – A request for price may not always include a target price. If a target price is not supplied, comparisons can be made when the costs are compiled. These may be either a comparison with similar work packages under manufacture or an assessment of competitor’s prices. This approach provides an overall view of the proposal’s competitiveness.
Once the price has been decided within a competitive cost structure, it is time to consider other customer requirements. For example, what delivery programme is the customer looking for and over what time frame does the customer want a price. Do they want a price at 1996 economic conditions or a price for a delivery of a number of sets over a five year period? Exact requirements are usually identified within the request for price. Should the requirement be for an average price fixed over a five year period, then consideration must be given to:
- Rises in material and labour costs;
- Financing costs;
- Risks associated with the terms and conditions within which the suppliers and customer will operate.
Cost is the term used to describe the consumption of money. This case study provides a detailed analysis which identifies how information about costs are extracted from a business to produce a price for a customer. The use of costs in this way is necessary to provide information for control and decision making activities by senior management.