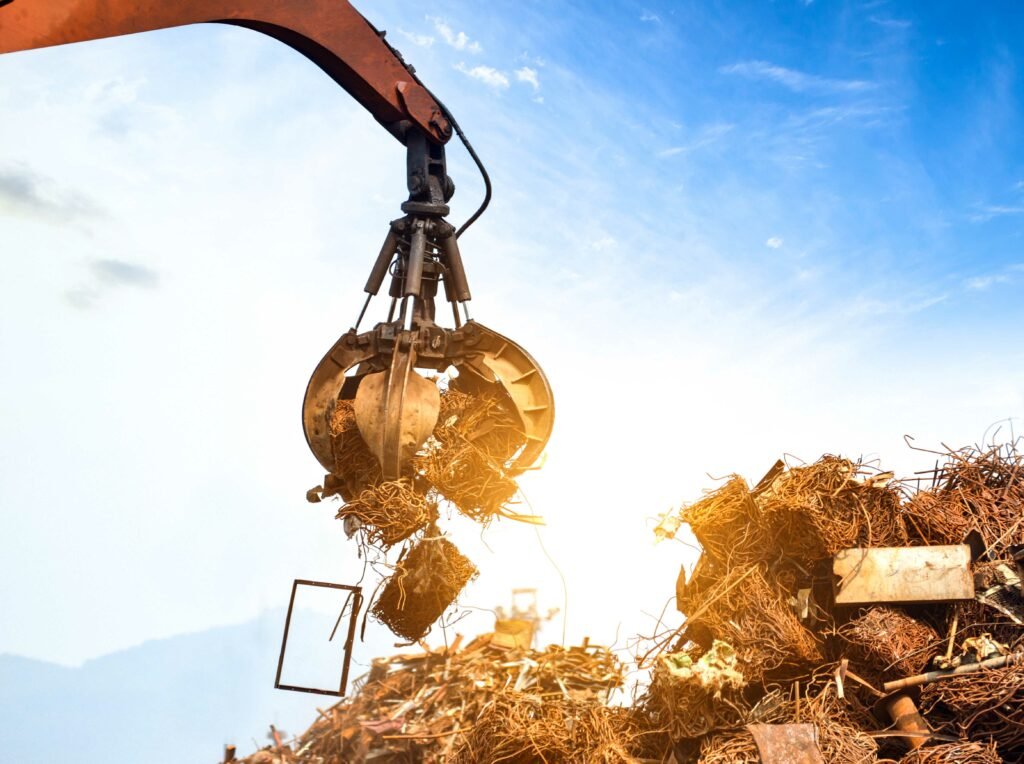
Scrap shears are industrial machines used to cut and process scrap metal into manageable pieces for recycling or further processing. They are crucial in the recycling and metalworking industries for efficiently handling large volumes of scrap materials such as steel, aluminium, and copper.
Choosing high-quality scrap metal shears, like those from Ing. Bonfiglioli is essential. They ensure efficient cutting, enhance safety with advanced features, and offer long-term cost-effectiveness, maximising returns for recycling and metalworking businesses.
Durability and build quality
Durability and build quality are critical factors in the manufacturing of high-quality scrap shears. These shears are typically constructed using materials such as hardened steel, which offer exceptional strength and resistance to wear and tear. This choice of materials is crucial because it ensures that the shears can withstand the rigours of regularly cutting through various types of metal without succumbing to damage or deterioration.
The use of hardened steel or other robust materials in manufacturing high-quality scrap shears is essential for several reasons. Firstly, it enhances the longevity of the shears, allowing them to withstand continuous use over an extended period without experiencing premature wear or failure. This durability is particularly important in harsh working conditions commonly found in recycling and metalworking environments, where shears are subjected to intense pressures and abrasive materials.
Additionally, the build quality of scrap shears plays a significant role in their reliability. Shears constructed with precision engineering and attention to detail are less prone to malfunction or breakdown, ensuring consistent performance even in challenging operating conditions. This reliability is crucial for maintaining productivity and minimising downtime, as businesses rely on the uninterrupted operation of their equipment to meet production targets and fulfil customer demands.
Cutting power and capacity
Selecting scrap shears with the right cutting power and capacity for specific materials is crucial for optimal performance in recycling and metalworking operations. Different types of metal vary in density, thickness, and hardness, requiring varying levels of cutting force to process effectively. Therefore, choosing shears with sufficient cutting power ensures efficient processing of a wide range of materials.
The cutting power of scrap shears directly influences operational efficiency by determining how quickly and effectively materials can be processed. Insufficient cutting power may result in slow cutting speeds, frequent jams, or incomplete cuts, leading to downtime and decreased productivity. Conversely, selecting shears with adequate cutting power enables smooth and swift processing, enhancing overall operational efficiency.
Moreover, the capacity of scrap shears, which refers to their ability to handle different sizes and volumes of materials, is equally important. Shears with larger capacities can process more significant quantities of scrap material in a single operation, reducing the need for frequent reloading and increasing throughput. This is particularly beneficial for high-volume operations where maximising efficiency is paramount.
The combination of cutting power and capacity also impacts the quality of the cut. Shears with insufficient cutting power may struggle to cleanly cut through thicker or harder materials, resulting in rough or jagged edges. On the other hand, shears with the appropriate cutting power can consistently produce clean and precise cuts, enhancing the quality of the processed materials. This is essential for meeting quality standards and ensuring the usability of the recycled or processed metal.
Maintenance and ease of repair
Easy maintenance and repairability are paramount considerations when selecting scrap shears. This will directly impact operational continuity and the lifespan of the equipment. By prioritising machines with straightforward maintenance requirements and ease of repair, businesses can minimise downtime and maximise productivity.
The accessibility of spare parts plays a crucial role in maintaining uninterrupted operation. Opting for models with readily available spare parts ensures swift replacement when components wear out or require servicing. This reduces downtime associated with waiting for parts to be sourced, shipped, or manufactured. This will allow for quicker repairs and minimal disruption to operations.
Furthermore, scrap shears with simple assembly and disassembly processes facilitate routine maintenance tasks and repairs. Easy access to internal components streamlines servicing procedures, enabling technicians to diagnose issues promptly and perform necessary repairs efficiently. Simplified assembly/disassembly also reduces the time and effort required for maintenance, allowing for more frequent inspections and upkeep to prevent potential issues before they escalate.
Investing in scrap shears with easy maintenance and repairability ultimately extends the equipment’s lifespan. Regular upkeep and prompt repairs ensure optimal performance and prevent premature wear and tear. Reducing the likelihood of costly breakdowns or replacements.
Safety features
When selecting scrap shears, prioritising safety features like protective guards, lock-off switches, and emergency stop functions is essential. Protective guards shield operators from moving parts and flying debris, reducing the risk of injuries. Lock-off switches prevent accidental start-ups during maintenance or tool changes, enhancing operator safety. Emergency stop functions provide a quick and effective way to halt operations in emergencies, minimising the severity of potential accidents.
These safety features not only protect operators from harm but also contribute to a safer working environment by mitigating risks associated with operating heavy machinery. By incorporating such safety mechanisms, scrap shear manufacturers demonstrate their commitment to prioritising worker wellbeing and reducing the likelihood of workplace incidents. Fostering a safety culture within recycling and metalworking facilities.