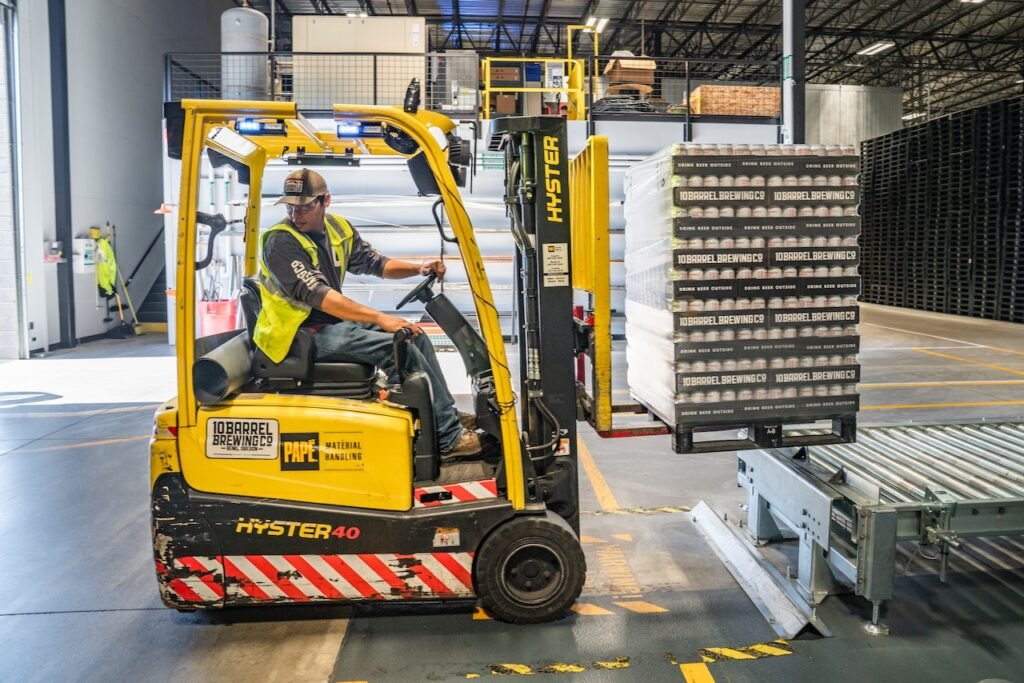
In the production process, various factors can limit the quantity and quality of output a producer can achieve within a specific time frame. These limitations are referred to as constraints on production, and they can be either internal or external.
External Constraints on Production
One of the primary external constraints is market size. A large market allows producers to operate on a larger scale, which can lead to economies of scale—a significant factor in reducing the cost per unit. For example, companies such as Cadbury (confectionary), Gillette, and Bic (razors) can produce goods in mass quantities due to the size of their respective markets. Larger markets provide the opportunity to streamline production, automate processes, and reduce costs per item. Mass production, in turn, often results in lower prices for consumers and higher profit margins for companies.
Another key external constraint is access to resources. For a producer to operate effectively, access to the right resources is critical. This includes raw materials, skilled labour, technology, and importantly, financial resources. Without sufficient funding, companies may struggle to invest in modern facilities or purchase essential machinery. For example, a manufacturing company that cannot finance new equipment will struggle to keep up with competitors that have modernised their production processes. Therefore, businesses often need to build strong relationships with financial institutions to secure the loans and investments necessary for growth.
Access to resources also includes securing raw materials and parts needed for the production process. If a company lacks reliable suppliers, it will face significant disruptions in production, leading to delays, missed orders, and loss of customer confidence. Modern businesses, like Nissan, have adopted strategies such as Just-in-Time (JIT) manufacturing, which ensures that materials are delivered exactly when needed, reducing waste and storage costs. However, for this to work effectively, the supply chain needs to be well-coordinated and reliable.
Internal Constraints on Production
On the internal side, one of the most significant constraints is the capacity of a company’s production facilities, including its buildings and machinery. A company’s ability to meet customer demand is often tied to whether it has enough spare capacity to handle new orders. If the current production line is at full capacity, additional orders may require expansion, new equipment, or hiring additional staff. Without room for growth, businesses may have to turn down new opportunities, stalling their potential for expansion.
Another internal constraint is the availability and skill level of the workforce. Modern production often requires highly trained and skilled labour, especially in industries that rely on advanced technology or specialised equipment. For example, the production of cutting-edge electronics or medical devices requires workers with specific technical skills. If a company lacks qualified staff, it can experience production delays, lower product quality, or even be unable to produce certain products at all. In such cases, companies need to invest in training and development programs to upskill their employees and stay competitive in a rapidly evolving market.
Additionally, time is a critical internal constraint. The ability to complete production processes within a given timeframe is crucial for meeting customer demand and maintaining efficiency. Proper planning and scheduling of production activities ensure that resources are used efficiently, avoiding unnecessary downtime or delays. Time management also involves ensuring that the production process aligns with customer delivery expectations. Companies that fail to meet deadlines may lose customers or face penalties, impacting both their reputation and financial standing.
Financial constraints are another important internal factor. Even if a company has the capacity and skilled labour, it may still struggle to meet production goals if it lacks sufficient cash flow. Companies require a steady flow of money to purchase raw materials, pay workers, and maintain equipment. Furthermore, investment in new technology or facilities is often necessary for expanding production capabilities, but this requires significant capital. Healthy cash flow and access to investment funding are therefore essential for maintaining and expanding production operations.
Importance of Addressing Production Constraints
Understanding and addressing these constraints is crucial for companies seeking to remain competitive. By overcoming both external and internal limitations, businesses can streamline their production processes, reduce costs, and increase efficiency. For example, by investing in lean manufacturing techniques, companies can eliminate waste, improve quality, and shorten production cycles. This not only helps in meeting customer demand but also in staying ahead of competitors who may still be dealing with inefficient production systems.
Addressing constraints also plays a role in supply chain management. Efficient supply chain practices ensure that raw materials and components arrive at the right time and in the right quantity, preventing production bottlenecks. Companies that focus on improving their supply chain relationships often experience fewer disruptions and lower costs, contributing to overall production efficiency.
Furthermore, overcoming financial constraints through effective budgeting, financial planning, and securing external investment can unlock new opportunities for growth. For instance, a company may seek to expand into new markets or increase its production capacity to meet growing demand. Securing the necessary funding allows the business to invest in new technology or additional production lines, making it more agile and responsive to market changes.
Conclusion
In summary, the constraints on production are multifaceted, ranging from external factors like market size and access to resources to internal factors such as production capacity, skilled labour, time management, and finance. Each of these factors can limit a company’s ability to produce efficiently and meet customer demand. However, by addressing these constraints, companies can unlock significant growth potential, achieve economies of scale, and increase profitability. In today’s highly competitive global market, businesses must continuously assess and address their production constraints to remain viable and successful.