Rapid prototype manufacturing is playing an important role in product development. Prototype parts can verify the appearance, structure and function of the design before it is going to mass production. There are four popular methods to manufacture prototype parts:
CNC machining, 3D printing, vacuum casting and plastic injection moulding, like the one Nordell is offering. CNC machining and 3D printing are often compared but there is still inclusive because they all have their own advantage and disadvantage.
Here I will focus on discussing the prototype parts produced by the urethane-vacuum casting.
Characteristic
Generally speaking, urethane-vacuum casting is a good method that can make high-quality prototype parts which are formed from inexpensive silicone moulds. Copies made in this way show great surface detail and fidelity to the original master pattern.
- The biggest characteristic of urethane-vacuum casting is fast. Liquid silicon can be solidified at room temperature. The silicon mould can be completed in less than a day or more than a few days. At the same time, modifying the silicon mould is also very convenient, which is conducive to greatly shortening the new product trial production cycle time. In addition, due to the flexibility of the silicone mould, the concave and convex parts can be directly taken out after casting. If the customer provides a master pattern, the vacuum casting can be finished in 3-5 days. If there is no master pattern, the whole cycle of rapid prototyping will only take about one week, which is more suitable for trial production and low-volume production.
- Low cost. The silicon mould can completely copy the characteristics of the master pattern, such as the surface effect, without too much post-processing, compared with the rapid prototyping of a single part, greatly saving the cost. And the silicon moulds can be durable for 20 or more copies.
Material selection
For plastic prototype parts, materials are widely selected. Materials with different properties can meet the requirements of prototype parts with different properties:
Transparent prototype parts: choose transparent PC, PMMA, and then polish
Wear resistant prototype parts: POM can be selected
High-toughness prototype parts: PA or PP can be selected
High-temperature prototype parts: Bakelite can be selected
Conventional product prototype parts: usually choose ABS, which can be split and glued, with a variety of post-treatment.
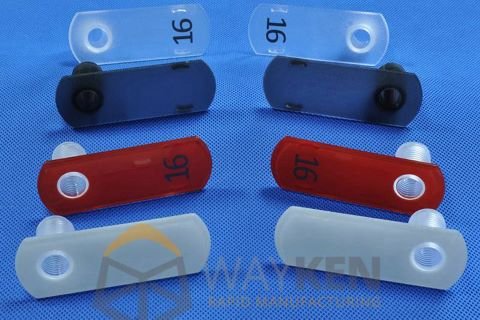
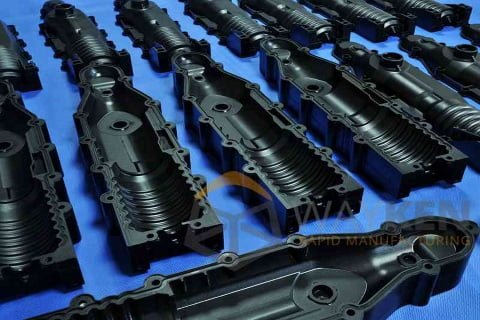

For urethane-vacuum casting, hundreds of casting polyurethanes are commercially available to copy any conceivable hardness and surface texture. Your design requirement has decided on the shape of the parts whether they are fully opaque, translucent or completely transparent. Due to its diversity of performance, similar to engineering plastics, as shown in the figure below, it is still unrestricted when making prototype parts in low-volume production:
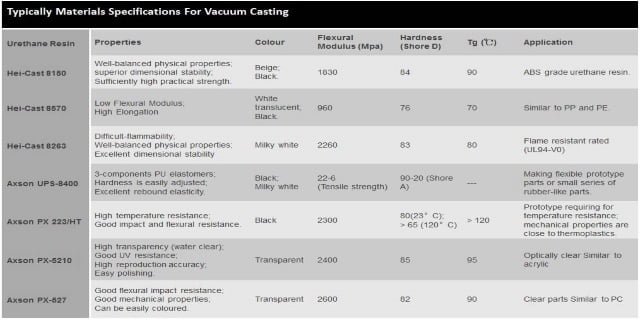
Process
Master pattern making:
If the customer does not provide the master pattern, we can use CNC or SLA process to make the master pattern quickly and polish is also available so that the casting products can completely maintain the same surface as the master pattern. If the number of prototype parts is large, there will be more corresponding silicon moulds. At the same time, 1-2 more master patterns can be made, which can be carried out simultaneously and shorten the production cycle time.
Silicon mould making and casting:
1. Mix liquid silicone and curing agent in proportion to weight and pour into the box where the master pattern is placed
2. After the liquid silicon solidifies, cut with a blade
3. Choose a suitable two-component polyurethane. Weigh component A and component B in a proper proportion and put them into a vacuum chamber, which purpose is to remove the water in polyurethane.
4. Put AB solution and silicon mould into the vacuum chamber, stirring AB solution while vacuuming it.
5. When the bubble of AB solution becomes less, pour it into the silicon mould in a vacuum state.
6. After pouring, slowly vent air into the vacuum chamber, which purpose is to fill the silicon mould with AB water with the help of atmospheric pressure. When the vacuum chamber returns to the atmospheric pressure state, take out the silicon mould.
7. Separate the mould, take out the prototype parts, and cut off the sprue gate.
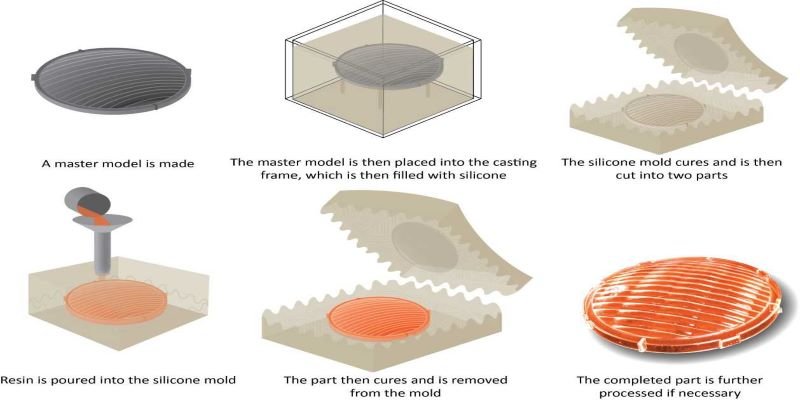
Matters and attention
1. After the mixing of liquid silicon and curing agent, vacuum extraction to the exhaust bubble should be carried out for no more than 10 minutes. If the time is too long, the liquid silicon will immediately solidify and produce a cross-linking reaction, which makes the silicon become lumps and unable to be coated or casting.
2. Before opening the silicon mould, polish and clean the mould smoothly, and then brush the mould release agent evenly.
3. If the silicon mould is used in small or fine surface prototype parts, soft silicon should be used, because the precision products are easy to be damaged in the process of demodulation. For large products, it is recommended to use silicon with high hardness to ensure that the mould is not easy to deformation.
4. It is better to leave the silicon mould for 24 hours after making it so that the performance of the silicon mould in all aspects will be very stable.
5. If the prototype parts have the requirement of colour. We need to deploy colour when mixing the two components of polyurethane, different batches of vacuum-casting prototype parts will exist colour differences, which is difficult to avoid.
6. The finished dimensions of vacuum casting prototype parts are dependent on the accuracy of the master pattern, the part’s geometry and the selection of casting material. Generally, a shrinkage rate of 0.15% is to be expected.
Conclusion
Different rapid prototyping manufacturing processes correspond to the different effects of prototype parts, when you need the number of dozens or even hundreds of prototype parts for small batch tests, vacuum casting is a good choice not only cheaper but also time-saving. Wayken has rich experience in this process, please be assured to provide us with your project, we will carefully evaluate and not only make high-quality prototype parts but also offer a full line of finishing services including painting, sandblasting, polishing and more. We’ll help you create prototype parts for exhibitions, engineering tests, crowdfunding, etc. For more information, please welcome to visit the website: https://www.waykenrm.com/