
In recent years, many UK manufacturing and service industries have transformed their production methods and processes. Businesses that have been at the leading edge of change have prospered, leaving their competitors behind. Key ingredients in this process of change have been an emphasis on creating total quality systems that involve:
- getting it right first time at every stage of production
- lean production to cut out waste and to simplify manufacturing systems
- creating environmental management systems that guarantee:
- the highest levels of environmental performance within an organisation
- excellent relationships with the local community.
Today, the Halewood plant is dedicated to producing the new Jaguar X’ Type. This is a car for the 21st century. It has been developed as a result of feedback from a massive global consumer research programme. The programme has ensured that the car’s designers, engineers and marketers remain in tune with the needs and expectations of potential customers at every stage in the car’s development.
This case study examines ways in which Jaguar has transformed its new assembly plant at
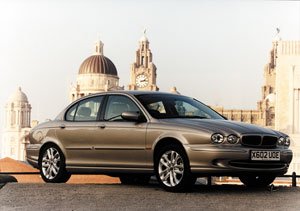
Halewood to guarantee World Class Performance in its production systems.
Developing the site
In January 1960, Ford bought the 1390 hectare greenfield site in Halewood from Liverpool corporation and the British Transport Commission. The Halewood site quickly became established as a leading car manufacturing plant and was associated particularly with Ford Escort production. When Ford acquired Jaguar in the early 1990s, Halewood also began to produce body panels for Jaguar cars.
In 1998, Halewood was announced as the production site for the all new Jaguar X’ Type sports saloon. It would replace Ford Escort production, which was to be phased out by 2000. Halewood was chosen to produce the X’ Type because:
- existing Jaguar plant in the Midlands lacked sufficient capacity
- the ‘Britishness’ associated with Jaguar made overseas production inappropriate good transport infrastructure
- opportunity to develop business park.
However, it was clear that the Halewood plant would need to be dramatically updated and upgraded if it was to become a world leader. So £300 million was set aside to modernise the plant. Coupled with this was a programme for changing ways of working and also the culture within the plant. Many Halewood employees had previously produced Ford Escorts using
traditional manufacturing techniques that did not encourage them to show initiative. They have now learned new approaches that involve empowerment and flexibility; more responsibility has been given to operatives at the sharp end of production.
Halewood’s refurbishment process involved replacing almost all of the production facilities so as to:
- deliver the exceptional quality levels required for a premium sports saloon
- create a highly efficient ‘lean manufacturing’ environment.
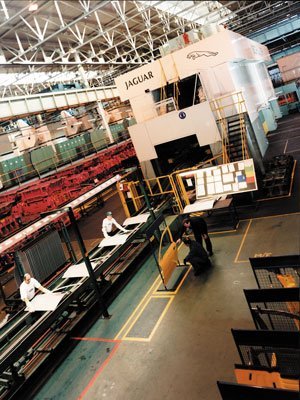
The plant’s productive efficiency has been further improved by developing a new Supplier Park alongside. Totally new production lines have been installed in Body Construction and for the Trim and Final area, with the latter abandoning floor conveyors in favour of overhead conveyors as part of the overall drive for improved production quality. The Press Shop has been fully refurbished. Two state-of-the-art computerised measuring machines have been installed to ensure the dimensional accuracy of the metal stampings. In the Paint Shop, 70% of the equipment has been replaced to deliver the renowned smooth and glossy finish of Jaguar’s four-coat paint system used in existing Jaguar plant. Months of planning were required to ensure that all the different building and installation activities could be achieved simultaneously within the product development programme.

The transformation of the working processes, environment and culture at Halewood started two and a half years prior to phasing out the Escort. A key priority was to transform a ‘them and us’ view of management held by many Halewood employees. The first stage in the strategy for overhauling customs and practices was the production of the ‘Halewood Vision’. This is a statement outlining the principles involved in creating a world-class manufacturing facility. A new set of working relationships was agreed with employees and each employee received a copy of what became known as the ‘green book’, which set out the operating principles required to move the business forward.
Three pillars for successful change


Line operators were given responsibility for identifying continuous improvements that could be made. Operators were organised into smaller teams working with a group leader. These groups have been given considerable responsibility for identifying a need for change and then driving it through. By being given experience of production methods in Jaguar’s leading edge plants in the Midlands, Halewood operators and group leaders learned more about the changes required.
The Centres of Excellence pillar was seen as the key driving force in changing people’s thinking. Bringing a large plant like Halewood to the required level of performance in a single leap would have been too great a task, so the concept of ‘Centres of Excellence’ was born. Under this, manufacturing improvement could be made first within smaller areas through close co-operation and teamwork.
As the established Centres of Excellence demonstrated progress, the concept was rolled out across more and more areas, until all the Centres of Excellence linked together and standards across the whole plant were transformed. Initially, just five showcase Centres of Excellence were established in March 1999. Each participating workgroup took responsibility for generating improvements through a specified series of actions, including:
- standardised work processes
- improvements to component delivery at line-side
- a ‘right first time’ approach
- a ‘best-in-class’ vision for general housekeeping.
The most obvious difference that this created was better cleanliness and tidiness. Line-side ‘cardboard cities’ were cleared away, as new racking and packaging – some designed by the operators themselves – was introduced to improve delivery to the production lines and to ease component picking. Benches and lockers were relocated into purpose-built rest areas and better floor surfaces were laid where necessary. In one of the initial Centres of Excellence, the entire working area, including overhead conveyor systems, was completely rearranged to a much more efficient layout designed by the section operators themselves, aided by engineering colleagues.
Efficiency and quality
The improvements in efficiency and quality generated such enthusiasm that by the end of 1999 Centres of Excellence were established for 30% of the workforce. By the time Escort production ended in July 2000, the concept had been extended throughout the plant.
Centres of excellence not only led to dramatic increases in productivity at Halewood, but also to increased pride and commitment within the workforce.
The Culture change programme was the third pillar. This involved over-hauling existing attitudes and ways of working to create an environment in which employees were encouraged to take ownership so that they became involved in managing the process of continuous change revolving around ‘lean production’. Implementing the Culture change programme involved creating a series of workshops for managers, union representatives, supervisors and line workers based on creating a new environment based on participation and empowerment. These workshops communicated the concept of the ‘Halewood Difference’ programme, based on supporting employee involvement in decision-making about production and production processes.
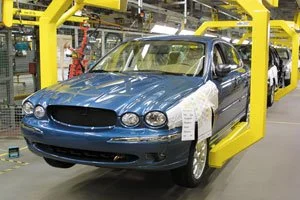
As part of the drive to create world class performance Jaguar recognise the importance of creating standards which best meet the needs of the wider community. This thinking is behind Jaguar’s focus on meeting the requirements for a healthy environment. The new car is based on company standards that prohibit the use of substances that have an adverse environmental impact. In addition, the car’s design is such that it meets the stringent requirements of the toughest exhaust and evaporative standards in the world. In preparing Halewood for the new X’ type, Jaguar set out to make the production process cleaner and more environmentally efficient than ever before. New initiatives included:
- introducing new, cleaner Paint Shop facilities and water-borne processes
- eliminating expendable component packaging
- creating a new Supplier Park next to the plant.
At the same time, improvements have been made to Halewood’s working environment, including better lighting, heating and ventilation. The plant’s energy consumption has also been reduced. A materials usage strategy has been adopted at Halewood which aims to
use only 100% durable, reusable, returnable packaging within the manufacturing process.
Commitment to the community
Jaguar’s commitment to the community is also strongly in evidence at a local level. Jaguar is developing relationships to integrate Halewood into the local community and the whole of Merseyside. Community Relations is a key part of the organisation’s corporate philosophy. This approach is exemplified in the process of re-skilling the Halewood workforce. As part of the overall training programme, over 800 employees spent a week involved in local community projects. These involved employees in:
- helping elderly local residents in pruning and redesigning their gardens
- designing and creating a school garden area
- helping to restore the grounds of a local church.
Jaguar employees are thus able to feel part of a caring organisation with a commitment to setting world class standards that cover all areas of production. They also know that wider aspects of running a world class business including concern for the environment and the local community.
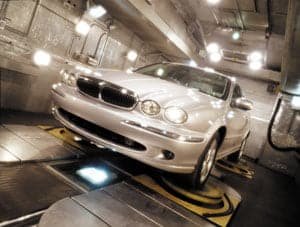