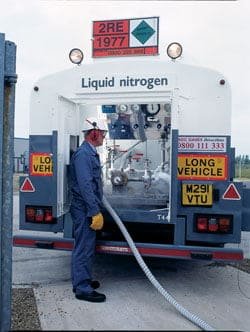
Living is a risky business. Taking risks begins in childhood, and continues throughout our lives and into old age, when many accidents are associated with confusion and forgetfulness. Sometimes we are aware of the risks we take; other times we are not.
The likelihood of personal harm, even disaster, in our lives is often influenced by:
- where we live
- our lifestyle and the company we keep
- our own attitude to risk
- the attitude to risk taken by others eg our employer, our favourite café, our local train operator, our local hospital
- our hobbies, interests and pursuits
- our job and the duties associated with it.
Life’s risks are shared unequally: we are not all equally exposed to risks associated with polluted air, damp housing, excessive noise, busy roads, rotating machinery, angry bulls, large crowds, severe floods, or engine failure in light aircraft.
This case study concentrates on risks in the workplace and examines how a famous company has set out to minimise them in the case of its own potentially hazardous industry.
The BOC Group
Founded over a hundred years ago, The BOC Group now employs over 40,000 people in some fifty countries around the world. Its major business is the supply of industrial gases to industries as diverse as semiconductor manufacturers, food processors and petrochemical producers. It is the world’s second largest industrial gas supplier and one of Britain’s truly world class companies.
Risk avoidance and reduction
We can reduce the number of incidents that affect health, safety and the environment when we understand their cause. This is particularly true of incidents that result from human error or from a failure to take adequate precautions against risks.
Creating a safer and less environmentally harmful workplace is, therefore, a learning experience that involves:
- finding out more about the risks associated with activities
- understanding better why accidents happen or environmental incidents occur
- reducing or eliminating the factors that contribute to risk.

Sometimes, hard lessons are learned only through bitter experiences. In 2001 in the USA, a young boy visited a hospital to have an MRI (magnetic resonance imaging) scan. Someone inadvertently brought an oxygen cylinder into the scanning room whilst the scanner was operating. The 10-tonne scanner immediately magnetised the cylinder. It was drawn into the machine and struck the boy on the head, killing him.
The gas industry is potentially hazardous. Its products can be toxic, oxidising, irritants, corrosive, flammable or asphyxiants. Gas production also often involves very low temperatures and very high pressures in gas cylinders. Transporting gases also has its hazards and difficulties.
The industry therefore gives a very high priority to health, safety and environmental considerations. Health and safety policies must become part of a business’s corporate strategy as well as part of its everyday operations. However, each business has limited resources to apply to health and safety policy. It must therefore use its resources very efficiently.
The importance of health, safety and environmental management
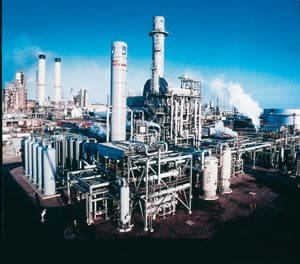
There are risks associated with every workplace. In some industries, the outcome of a typical incident may be relatively slight, for example an office worker shaken and upset by slipping on a wet floor. In other industries a typical incident can have far more severe consequences, such as a farmer pinned beneath an overturned tractor, a building worker hurt in a fall, or a factory worker caught up in machinery.
Industrial accidents create not only personal grief and distress but also huge financial costs and unwelcome negative publicity for the organisation and industry concerned. They are of great interest and concern to all of the organisation’s stakeholders eg employees, managers, shareholders, local residents and businesses, and suppliers.
In a modern society, people will not allow organisations to ignore the impact of their activities on surrounding communities. Not all of the stakeholders have the same interests. In meeting their health, safety and environmental responsibilities, businesses have to strike a balance between conflicting interests. When a firm puts forward a safety recommendation, its shareholders will want to know the cost of implementing it, whilst employees are more likely to ask how many illnesses, injuries or deaths it is likely to prevent each year.
Before the introduction of health and safety legislation, there was always the possibility that irresponsible or unscrupulous employers might view health and safety issues as a low priority and so set very low standards. When, in the UK, voluntary codes of practice failed to produce acceptable standards across all industries, they were supplemented by laws and regulations set by the UK government and the EU. These set out employers’ duties and responsibilities.
The Health and Safety at Work Act, passed by Parliament in 1974, sets out the duty of employers to ensure the safety and welfare at work of all employees ‘so far as is reasonably practicable’. The Act also imposes obligations on employees to have regard for the health and safety of themselves and others. In the UK, a number of health and safety regulations as well as environmental laws and standards have also been brought in to comply with EU Directives. Today, socially responsible organisations go beyond these standards. They monitor and evaluate their performance and develop approaches to health and safety that reflect best practices across each industry in which they operate.
Risk management
Risk management is a process that attempts to identify and understand specific risks within the business, and to identify the cost of reducing or eliminating those risks. The BOC Group faces both direct and indirect risks. Direct risks arise from the business’s core operations and may come from:
- environmental incidents, such as greenhouse gas generation or the production of wastewater
- health and safety incidents affecting a range of groups both within and outside a plant.

Indirect risks follow on from direct risks. They include damage to a firm’s reputation and the adverse media attention created by a high profile incident. Companies with poor accident records may run the risk of losing favour with investors and finding it hard to raise funds. These are also indirect risks.
Within The BOC Group, managers have the key responsibility for safety and for environmental management. Their performance is measured and evaluated, for instance by how they minimise waste in the use of energy.
In recent years, The BOC Group has invested heavily in extending safety measures and in improving environmental performance. As a result, accident rates have been falling and the Group’s production and distribution processes have become increasingly efficient.
The BOC Group operates in some 50 countries. Each country has its own statutory regulations for health, safety and the environment which may or may not overlap with UK and EU requirements. Additionally, different cultures and languages provide further challenges.
Although The BOC Group provided policies and manuals that took into account the local geographies, conditions and regulations of operations within each country, the different interpretations and systems had the potential to cause confusion.
Adopting best practice
The solution to this problem is ‘best practice’. BOC decided to integrate all of its policies and manuals and to go beyond the statutory requirements of each country in which the Group operates. This involved establishing global teams to create best practice standard benchmarks that would bring all operations to the highest possible levels.
The movement towards best practice meant doing more than simply complying with regulations and training employees in safety, health and environmental management. It meant coaching and training employees to give them a much deeper understanding of the issues involved. The aim was to influence the hearts and minds of BOC employees so that working safely and protecting the environment became second nature to them. Employees in all of BOC’s businesses underwent a competency-based training programme that enabled them to perform work-related activities to high-specified standards.
Safety, Health and the Environment (SHE) policy
The Group’s SHE policy emphasises that for The BOC Group, safety, health and environmental management is the highest priority. It is also an area in which the Group looks for ongoing improvement. SHE affects corporate strategy at the highest level and also everyday operations.
BOC managers are required to achieve ongoing improvement by:
- maintaining sound operating practices, including a planned approach to risk
management and the measurement of health, safety and environmental performance - promoting the sustainable development of their businesses
- ensuring high standards of training, information and supervision by providing support and encouragement at all levels.

For The BOC Group, its SHE policy is a declaration that it takes its wider responsibilities seriously. The policy has created a system of continuous improvement that constantly updates and develops employees’ :
- actions
- responsibilities
- behaviour.
These elements are broken down and expressed in more detail in BOC’s Integrated Management Systems and Standards (IMSS). It defines BOC’s worldwide management responsibilities and the organisational arrangements for safety, health and environmental management. IMSS refers to highly specified technical information in relation to, for example, flue gas or the disposal of catalysts. In each case, the system provides detailed information on how to deal with a range of associated hazards.
Providing highly specified information about a range of hazards within the working environment is a key element in improving health and safety. When understood, taken seriously and acted upon, it can save lives, as John Porter can testify.
BOC employee John Porter had been making regular deliveries of liquid nitrogen to the Scottish Blood Transfusion Service. On one visit, the gauges showed ‘empty’, but as he filled the tanks he was told that a delivery had taken place the previous day. The gauge was in fact faulty and excess nitrogen had escaped through a relief valve causing an asphyxiation hazard. When he went to check the tank and switch off the valves, he was overcome and passed out. The proximity of other employees who had been trained both in the use of breathing apparatus and the correct emergency procedures saved his life.
Conclusion
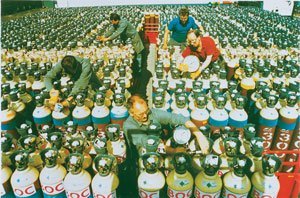
The BOC Group sees its Safety, Health and Environmental policy as the right and proper way to achieve its objectives of extending safety measures and improving environmental performance. The policy has helped to provide guidelines that enable all its employees to focus on how to develop best practices over and above statutory requirements around the world. The SHE policy is an ongoing and updateable document that can raise standards even higher in the years ahead.