
Walkers are the UK’s biggest crisp manufacturer. The business operates the world’s largest snack factory at Bursom Road, Leicester.
Walkers had a humble origin, Mr Henry Walker started out as a butcher in the 1880s, and created a successful business in Leicester and Mansfield. By the 1940s, World War II had seen the introduction of strict meat rationing and by 10 am shops had sold out. The business was working at only half capacity and so diversifying the business had to take place. In 1948, Walkers began manufacturing potato crisps.
Walkers is now a subsidiary of the worldwide PepsiCo group, which is a multi-branded New York based corporation. The business operates in almost 200 countries with 153,000 staff and has operated in the snack foods market since 1966. In the UK, Walkers employs over 4,000 people in 15 locations.
The Walkers brand is the market leader in the UK, with its head office based in Berkshire. The sales & marketing forecasting team plans and determines the levels of output that is required at the factory. The Walkers factory in Leicester employs over 2,000 people. Many of them are specialists and include quality, engineers, safety officers, financial, operations and planning managers.
The sheer breadth of expertise shows the scale of the business. The factory operates its own P&L, that is to say, it has a standalone budget that has to be met or bettered. This means its managers have to make decisions based on what is best for its particular operation. As the factory works on such a large scale, there is scope for considerable profits or losses.
This case study will examine how the Walkers processing plant works and show how it contributes successfully to overall group profits. It operates to achieve a balance in four key areas:
- safety
- quality
- customer service
- cost.
By managing these, the factory intends to meet the needs of all customers, as well as its own.
Safety
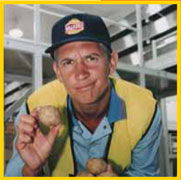
The International Labour Organisation (ILO) tells us that globally there is one death in the workplace every 15 seconds, and almost 270 million accidents happen each year. In the UK, the government Health & Safety laws place a ‘duty of care’ on both employers and employees.
Walkers are fully aware that factories are dangerous places. They contain machinery, sharp instruments, slippery floors and a great deal of noise. This means that there are many risks to staff.
Walkers, therefore, regard safety as their highest priority and have a particular goal regarding safety. It believes that workers should walk into its factory fit and well and leave it the same way. A worker fatality is the only occasion where the President of PepsiCo, the Parent Company, must be informed within 2 hours, wherever she or he may be in the world. This demonstrates the company’s commitment to safety as its No.1 priority.
Managers at the Walkers factory know that their job is to keep staff safe on site. To do this they must assess the levels of risk that workers face in the factory. They know all the processes involved in crisp manufacture. The operatives who work machinery learn to follow strictly controlled methods in a way that risks are guarded and danger reduced.
There is a culture of safety at Walkers, this means that safe working practices take priority over others, even customer service. If production has to stop to repair a faulty and dangerous machine, it happens – even though this may lead to a delayed delivery for a customer. Due to its vigilant attention to safety, Walkers has an excellent Health & Safety record. The Health & Safety Executive uses the factory as an example of good practice.
Quality

Quality, in the eye of the consumer, means that a product must provide the benefits required by the consumer when it was purchased. If all the features and benefits satisfy the consumer, a quality product has been bought. It is consumers, therefore, who define this.
Walkers prides itself on the quality of its products and are aware that if its crisps do not meet consumer expectations, people will buy an alternative product. As Walkers make and sell 11 million packs per day, a drop in demand is one indication of a lack of quality in the Walkers product. The company is committed to working to maintain and improve standards at all times.
Walkers maintain a comprehensive approach to quality known as TQM (total quality management). There is a ‘quality chain’ involved with potato crisps. From the first basic ingredient (the potato) through to all of the procedures involved in creating a single crisp, processes are there to ‘assure’ quality. This is ‘quality assurance’ – doing things that are most likely to build quality into a product.
Walkers’ approach to quality involves looking at the whole supply chain, starting with the farmers who grow the potatoes. The company supplies the seeds to ensure quality – only the very best potatoes go to make crisps. The farmers’ payment is measured against a quality scale, as the best potatoes with lower water content earn more.
Quality assurance requires that a supplier offers only the finest raw materials. Walkers specify the exact potato it needs and deal only with the best suppliers. The company policy is to trust suppliers and not to inspect every delivery.
In the factory, potatoes undergo washing, peeling, slicing, cooking, flavouring, packing and loading. Checks happen at each of these stages to make sure nothing goes wrong. This is called ‘quality control’. Representatives from the farms work within the factory to manage the processing of the potatoes. Each potato is sliced to a specific thickness, with each crisp automatically scanned and those that do not meet a specified standard are rejected.
Throughout the processing, a team of trained laboratory technicians take samples and measure them against a predetermined ‘Gold standard’ to ensure standards are rigorously maintained. Additionally, random checks are made on competitors’ crisps to see how they measure against the Walkers brand.
In any manufacturing business, getting the quality right is vital whilst operating as cost effectively as possible. Production methods must be well organised with wastage monitored closely. Waste costs money.
Customer service

The Walkers’ factory must meet the needs of several types of customers. Some of these are within the business, and some of them are outside it. The factory is answerable to its head office in Berkshire, which set sales forecasts. It also informs the factory of sales trends and market fluctuations.
Its head office is the plant’s ‘internal’ customer and it is vital for the continued success of the business that the processing plant responds to and meets the forecasts and trends that they provide. The factory has to be capable of stepping up production when required and be able to scale down too, if necessary. If the head office decides to produce certain flavours or combinations of flavours in different quantities, the factory must adjust production to meet these new demands.
Externally, the customers of the business are the many retail supermarket outlets selling Walker’s snack foods. Ultimately, the crisp lover is the final and most important customer. All the efforts in the factory must eventually satisfy the consumer. Walkers crisps must sell and this can only be achieved if they meet consumer expectations.
At Walkers, the aim is to deliver 98.5% of what a supermarket has ordered within 24 hours. When the product arrives at a store, it must have a ‘shelf life’ of at least nine weeks before the ‘best before’ date. The processes at the Walkers factory have to deliver exactly what customers need – every day. This means daily adjustments to mechanical loading. For managers and workers at Walkers, this is a challenge they have to meet.
There are 160 different variants of Walkers snacks and orders change constantly. To keep customers satisfied, it is important to get things right. Management must monitor buffer stock levels – products held to cope with variations in sales. Too much stock held awaiting orders is an unnecessary drain on costs, as is seen later.
The need to manage stock levels creates conflict between holding products to meet orders and producing at a level that matches sales. Managers have to consider ‘economies of scale’. These are savings per unit brought about by a larger volume of production. Each unit costs less the more that is produced. These facilities have to be balanced against the complex requirements of customers. When production is at its most efficient, it may not always result in meeting specific customer needs.
Cost
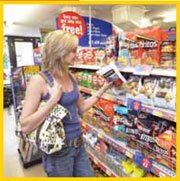
Each Walkers production factory is a separate reporting profit centre within the group. Management’s operational performance depends on maximising the output from the factory of the required products. A crucial aspect of delivering the highest contribution to company profit is the tight control of costs.
Walkers produce packets of crisps on a gigantic scale, so a diminutive saving on each one can produce enormous savings. All employees are encouraged to spot ways of saving on process costs, and efficient management of the production process is where lower unit costs occur.
One of the main drivers of cost is the efficient use of labour resources within the factory. If the production process starts to produce low quality products (which will automatically be rejected before it reaches the packing area) there will be a large labour resource associated with packing with very little to do and hence incurring cost. It is important that the processes keep within the defined high quality parameters.
The implementation of quality policies also saves on costs. As Walkers produces products to the highest standards, there is very little waste. Nor is there a need to redo work or procedures that have already been completed. From the consumer’s point of view, all efforts to deliver top-rate customer service mean that there are no returns or unsold stock.
The careful management of inputs into the production processes at the factory results in the resourceful use of materials. Walkers use a continuous flow production method. Materials are required to arrive at the point in production just-in-time. This means efficient use of labour, energy and plant, and there is no need for large holdings of stocks of raw materials.
The Walker’s production process works so that finished products move out of the factory and onto lorries for transport. Significant ‘buffer’ stocks awaiting orders aren’t required.
Conclusion
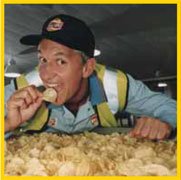
Operational management refers to the day-to-day administration of a business, and managers at this level have to make decisions about everyday processes. Through a system of accountability, each manager has to answer for his/her decisions.
Walkers is a subsidiary business within PepsiCo. Even within the UK group of Walker businesses, the Leicester production facility is a distinct profit centre. As an operation, it is a multifaceted business unit. As the world’s largest snack food plant, the factory is working on an enormous scale of production. Strategy is determined elsewhere, but managers on site make vital decisions on production which ultimately ensures the Walkers brand is always available to consumers for purchase.
Effective management of the plant depends on sequencing and balancing the four concerns outlined in this study. Each one needs attention and emphasis to differing degrees – Walkers refers to this as a ‘balanced scorecard’. Each of the key concerns is interdependent and close attention to quality leads to increased demand for the product.
Good customer service has the same effect, as people get to recognise and trust Walker’s crisps. Increasing demand, fluent production processes and continuous attention to safety and quality ensure that the Leicester plant operates at optimum effectiveness, which is vital to the continued success of the Walkers business. These things are at the heart of successful management.