The steel manufacturing company Corus focuses on meeting the needs of its worldwide customers and providing innovative solutions. It manufactures, processes and distributes steel and aluminium products worldwide.
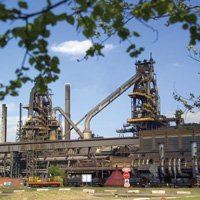
Corus is a subsidiary of Tata Steel, part of the giant Indian conglomerate. Tata Group includes businesses in many industries – for example, chemicals, automotive, telecommunications, leisure and consumer goods (such as Tetley Tea). Tata Steel acquired Corus in 2007 as part of a strategy of international expansion.
Steel is everywhere in our homes and all around us. Corus Construction & Industrial (CCI), a business unit of Corus, has steel manufacturing facilities in Scunthorpe, Teesside, Scotland and France.
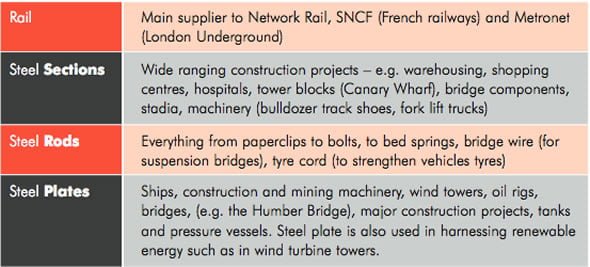
The key markets for CCI include construction, energy and renewables, engineering and machinery, mining and earthmoving equipment, shipbuilding, fastenings and rail. The principle manufacturing site at Scunthorpe covers 2,000 acres and employs 5,500 people. The site consumes 6.5 million tonnes of iron ore and 2 million tonnes of coal each year to produce 4.3 million tonnes of steel products. CCI products go into a range of leading edge developments.
The production process
Modern steel production is a large scale operation dealing in huge quantities of materials and products. The process of steel plate production has several stages:
- Receipt of pre-cut steel slabs from the steel plant
- Reheating of slabs
- Rolling to achieve required dimension and mechanical properties
- Initial inspection for surface or quality defects
- Cutting to order size
- Marking with unique identities
- Cold levelling to agreed flatness standard
- Final inspection
- Loading and despatch to customer
Producing large volumes helps to drive down the costs of running huge and expensive steel plant. Overall, this results in steel being a relatively inexpensive product, typically around 50 pence per kilogram, about the same as a kilogram of potatoes.
In a major building project, such as a shopping complex, the cost of the steel can be as little as 5% of the overall cost of the project. Because of these issues, CCI needs to differentiate its business from its competitors in order to continue to grow.
CCI’s business strategy is to produce quality steel to satisfy customer requirements, focusing on delivering products at the right time in order to secure profitable business. A key challenge is to meet the increasing demands for more steel, at increasing levels of quality and to comply with more demanding delivery requirements.
It would be straightforward to meet these challenges using brand-new facilities. However, a new ‘greenfield site’ steel mill could cost more than £300 million to build. CCI therefore needs to make process efficiencies and quality and delivery improvements with its existing manufacturing plant. This presents challenges when older facilities are not well structured to use modern manufacturing techniques and processes.
This case study focuses on the process of Continuous Improvement (CI) at the CCI steel plate manufacturing mill at Scunthorpe. It will show how Corus is finding new ways of achieving its objectives from existing resources.
Continuous improvement
Continuous Improvement is often referred to by the Japanese word ‘Kaizen’. Kaizen means ‘change for the better’ and covers all processes in an organisation. These include engineering, IT, financial, commercial and customer service processes, as well as manufacturing.
CI involves making continual small improvements to a process rather than big changes at irregular intervals. This requires close monitoring and control, changes to the uses of manpower, machinery, methods, materials and money to improve business efficiency.
Continuous Improvement starts with management and under their leadership works down through the organisation. The underlying theme is that everyone is responsible and has a part to play in making improvements. All employees must work together to identify the steps needed to improve working practices. Planning meetings help teams to focus on satisfying customer needs. Visual management techniques, such as flow charts and wall charts make clear what resources are necessary and who is responsible for each part in the process.
Reducing waste
Everyone has the opportunity to eliminate waste. This is any activity or process that does not add value. A key question to define waste is ‘would a customer pay for that process?’
There are seven main areas of waste for any business:
- transportation – moving materials or products about
- inventory – keeping too much or the wrong stock
- motion – people moving or travelling excessively
- waiting times – allowing products to wait for processing
- overproduction – making too much
- over processing – doing too many processes during manufacture
- defects – errors or flaws in the product causing rework or needing to be scrapped
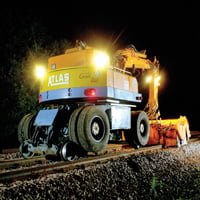
Production processes that minimise waste are referred to as lean production’. In these processes, the aim is to use less of everything, for example, space, materials or time.
CCI in Scunthorpe is looking to reduce waste in its plate manufacturing process. It has adopted the concept of ‘flow’. This means that the products are ‘pulled’ through the process according to customer demand.
All parts of the production process, from the supply of raw steel (slab) to the finished steel plate, are carefully planned. Scheduling for each element of the process ensures that bottlenecks are kept to a minimum. Each process is paced (known as ‘takt’ time) to control the amount of product in each stage of the process. This ensures that processes operate smoothly without overload or delay and keep the desired output and quality.
Tonnage was the traditional key measure of productivity for CCI. For employees to work to a smooth paced process needed a significant culture change.
Implementing a continuous improvement culture
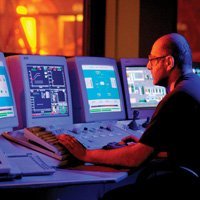
A CI culture means that everyone can put forward ideas and have a say in how processes can change for the better. This is known as engagement.
CI needs teamwork. In Scunthorpe, a CI manager coordinates the process. 40 CI Coaches chosen from the workforce received training to facilitate improvements. CCI has put together a ‘toolbox’ of techniques which the coaches use with managers, employees and operators. These help everyone understand where and how they can improve their work.
An organisation needs to know where it is going in order to be able to put in place the resources it needs to achieve its plans. This is set out in a vision.
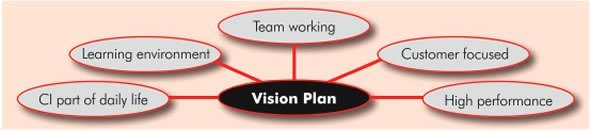
Scunthorpe plate mill has set out a 5-year vision improvement plan which will help in the process of developing a CI culture for the business. Everyone in the organisation has to understand and actively support the plan. Workshops for all employees have taken place to explain the vision and why the change is necessary if CCI is to remain competitive.
Process mapping
Helped by the CI Coaches, workers have drawn maps of their processes. These show the links between the stages of manufacturing as well what information flow is needed. The maps show:
- details of tonnages
- number of products
- rework cycles
- inspection points
- stocks
- delays
- costs
The first part of this process is a ‘current state value stream map’. This shows what the systems and processes are like now.
The next stage considers what the ‘future state map’ would look like. This highlights what CCI needs to do to achieve this state, for example, investing in new processes, equipment or additional staffing.
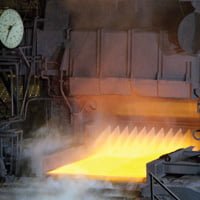
Scunthorpe plate mill has 16 system maps. These link to each other to give an overview of the whole process. For each of the 16 systems, a number of rules about stock levels and stock rotation have been set up:
- Stock rotation ensures that the plates for one customer do not become buried beneath others and therefore delayed.
- The required amount of slab steel (‘feedstock’) must be in front of the mill by the Tuesday of the week in which the material is to be rolled.
- By rolling plates in the planned week, the mill is properly paced and all ‘downstream’ processes (such as cutting, levelling and inspection) can be scheduled accordingly.
Using the value stream maps has helped CCI to improve process flows and the working environment. It has also reduced unnecessary motion, transport and processing.
By taking these small steps and involving everyone in the vision, the delivery of product has increased from 70% of plates on time to 92% on time.
Target setting
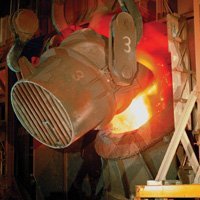
CI working requires everyone to think differently about the way they work. It was recognised that people might be resistant and cling on to old ways of working.
The key was getting all workers to see change as their responsibility. The CI coaches support the teams and individuals and promote or ‘champion’ new ways of working.
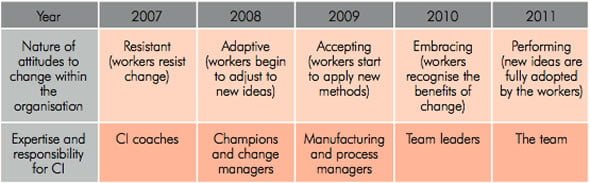
To help workers accept the changes, the 5-year plan established a timeline for the programme of introducing change. Over time, the team and individuals are empowered to take responsibility and make decisions for themselves.
Key performance indicators
An important part of the Continuous Improvement programme was the creation of Key Performance Indicators (KPIs).
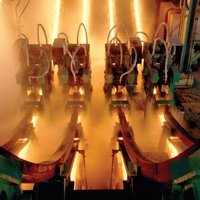
Previously, the only measure at Corus was the number of tonnes of steel rolled. This did not show whether it met customers’ needs or whether the steel needed rework because it didn”t meet customer requirements.
Corus has set new KPIs which focus on meeting customer deadlines, such as:
- a zero backlog of customer orders – this means customers always get their deliveries on time
- meeting targets for rolling steel plate in its allotted week
Corus monitors and measures how its operations compare with other producers and competitors in the steel industry. This process of benchmarking means that Corus is continually reviewing its activities to achieve best practice.
Corus shares relevant information both within and across Corus to drive improvement. It also spreads appropriate technical knowledge and information across the steel industry through international groups such as the International Iron and Steel Institute.
The benefits of continuous improvement
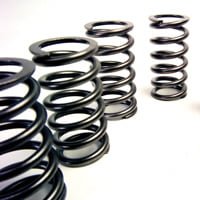
There are significant costs involved in setting up a Continuous Improvement programme, including:
- allocating employee time to participate in group work
- training coaches
- setting up a manual of tools and techniques
However, Corus is already seeing the benefits of CI with:
- reduced waste through lean production
- improved product quality
- reduced rework time
- faster response times, giving more customers their orders on time
- becoming more competitive by driving down costs
- retaining/gaining customers through innovative products and services.
By empowering its workers, Corus gains a more committed workforce which helps to drive further improvement.
KPIs show that the Scunthorpe mill is achieving its targets for rolling steel in planned weeks and is delivering almost 100% of customers’ orders complete and on time. Scunthorpe Plate Mill aims to have all orders complete and on time by March 2009, while at the same time reducing lead time.
The principles of team working help to create a more flexible workforce. This gives Corus the capacity to increase or change production when necessary. In addition, Corus employees are more likely to be satisfied and motivated when they feel that they are making a contribution. They can see their expertise helps to create a more effective company.
Conclusion
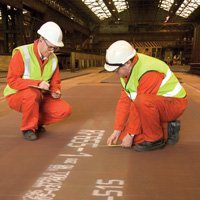
Corus is transforming production at its Scunthorpe plate mill through Continuous Improvement. This way of working encourages all employees to behave as team members to identify and support work improvement opportunities. Increasingly employees at every level are making improvement their responsibility, which provides employee job satisfaction.
Continuous Improvement helps Corus to provide quality products and services for customers with on time delivery. CI supports Corus’ aim to achieve satisfied customers and secure repeat sales and longer term orders.
It is part of a long term strategy based on service to develop the business. It aims to improve operational demands to fulfil customer expectations and out-perform competitors.