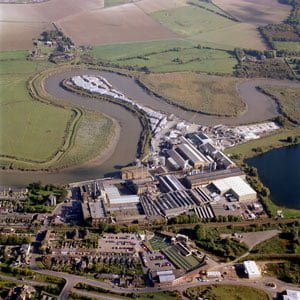
This case study examines the means by which the Jefferson Smurfit Group’s basic product – the box – is designed and manufactured, considering the ways in which value is added at each step of the process, and how, with the central importance of recycling, the Group’s businesses are conducted in an environmentally responsible manner. In the early 1930s, Jefferson Smurfit, Sr. saw the untapped potential of a small Dublin box factory and with the purchase of that firm, the story of the Jefferson Smurfit Group began.
Over the succeeding decades, the Smurfit Group grew rapidly, obtaining a listing on the Dublin Stock Exchange in 1964, the London Exchange in 1970 and the American Stock Exchange in 1983. Dr Michael Smurfit, son of Jefferson Smurfit, Sr. And Chairman and Chief Executive since 1977, has led the Group through a period of successful global expansion.
Today, the Jefferson Smurfit Group, together with its associates, is the largest paper based packaging organisation in the world. With more than 200 companies operating over 400 facilities around the globe, the Group employs more than 45,000 people in 25 countries. More than 60 reclamation plants around the world, processing more than five million tonnes of waste paper, make the Jefferson Smurfit Group the world’s largest recycler. And, with its research and development centres at Talence, France and Carol Stream in Chicago, the Group continues to develop the products and techniques which will ensure its industry leadership into the future.
Containment, protection and display
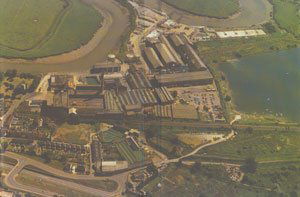
Just about everything we buy or use, at some point along the way, comes in a box. Why? Because boxes provide three basic benefits: containment, protection and display. Achieving these aims as effectively and efficiently as possible is the goal of box design and production.
Consider an apple. While it grows and matures on the tree, an apple is protected from the elements by a strong skin, which also holds together the seeds and nutrients which the apple contains. This skin is, in a sense, the ‘box’ which contains and protects the apple. When the apple ripens and falls to the ground, this skin disintegrates, releasing the seeds and nutrients into the earth. Thanks to the apple’s own natural packaging, its contents have reached their destination – in this case, the earth – safely, and with the disintegration of the protective skin, everything is returned to nature and nothing has gone to waste. It’s a very efficient and natural process, and provides a useful model for the environmentally-sound production of today’s man-made packaging. When an apple is picked and eaten before falling to the ground, we can say that the third benefit, display, has prevailed, because the apple looked good enough to eat!
Up until the mid-19th century, most packaging consisted of wooden boxes, barrels and jute sacks. Although these containers could be used again and again, they were heavy and unwieldy and with the tremendous growth of worldwide trade since that time, a lighter and more convenient type of packaging was clearly needed. With the mechanisation of paper production, it became possible to construct sturdy packaging from this material and the box we know today, made from recyclable paper products, was born.
Issues in box design
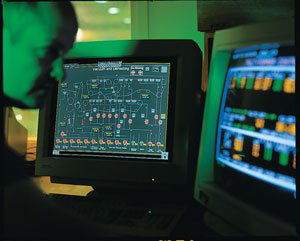
In designing a box, the elements of containment, protection and display – to varying degrees, depending on the use proposed – are paramount.
A product manufacturer, in consultation with structural and graphic designers, must consider the degree of fragility of the product, what stresses and hazards the product is likely to encounter in packing, storage and shipping and to what extent the display of the packaging will contribute to its attractiveness to the consumer. These criteria will influence the material, style and shape which the structural designer will choose for the finished package, while the graphics designer will concentrate on using the shape and texture of the pack to achieve maximum effectiveness at point of sale. In this way, a customer-driven packaging solution is obtained.
Structural designers will concern themselves with the specific requirements of shipping and storage, in order to match the appropriate materials to the performance levels required. If the product has a unique shape or size, these designers will assist in developing the exact shape of container which the product needs. Computer-Aided Design, or CAD systems, are used to specify and translate these requirements into a form which is usable on the shop floor where the box is manufactured.
When display is an important consideration, graphic designers – using Computer-Aided Graphics, or CAG systems – will also contribute, designing an attractive presentation of the product’s identity which will be printed on the board before it is cut, scored and glued into its final box shape. But let’s go back to the beginning. How and from what materials is a box manufactured?
The raw materials
Wood is the primary raw material used in the manufacture of a box. The cellulose fibres contained in wood are well suited to paper-making and certain species of tree provide fibres which are especially suitable for making the grades of paper needed for making boxes. Pine and spruce trees provide excellent raw material, but the long time needed to bring them to maturity – as much as 70 years – can be a drawback, as it is prudent and responsible to renew the natural resource of the forest at a faster rate than we consume it. As a result, more rapidly maturing species like eucalyptus – which reaches maturity in only seven to ten years – are increasingly important. After harvesting, the wood is turned into pulp by various processes of chipping, grinding and bleaching and is then dried and assembled into bales.
Recycling waste paper
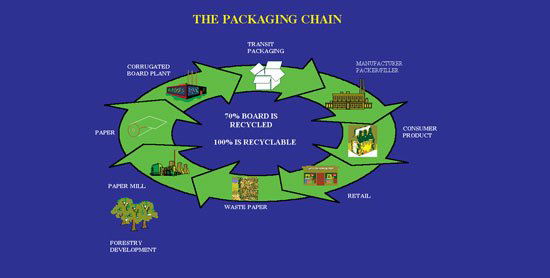
Waste paper is the second vital source for the fibre used in making boxes. This reclaimed fibre is known as secondary fibre, to distinguish it from the primary fibre which is provided by wood. Both types of fibre are needed and on average, 70 to 80 percent of the fibre used in the production of a box is this secondary, recycled fibre. Virgin fibre from wood pulp is always required, however, because with each recycling, the cellulose fibres become shorter and less resilient. The Jefferson Smurfit Group is the largest recycler of paper products in the world, reclaiming some five million tonnes of waste paper each year through over sixty recycling centres worldwide. Waste paper is sorted, graded and baled before use.
Making the paper
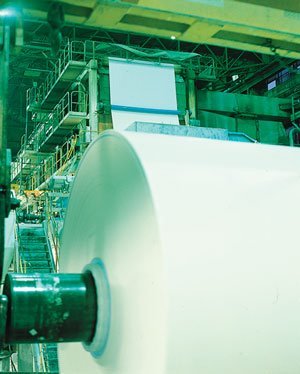
To produce the paper used in making boxes, bales of wood pulp and recycled paper are placed into a pulper containing water and a powerful agitator. This agitator breaks up the pulp and mixes it with water to produce a porridge-like solution called stock. More water is added and the stock is refined and screened to remove impurities. The solution at this point is 99% water and only 1% fibre.
This solution is then passed over a very long conveyor of wire mesh, which allows much of the water to drain away, leaving only the wet fibres on top of its surface. This part of the process is known as the ‘wet end.’
The wet fibres are next passed through sets of heavy rollers where more moisture is squeezed out and drawn away. The wet paper fibres are then passed through a series of dryers, where steam-heated rollers evaporate the last of the remaining moisture before the paper is gathered up at the other end in long rolls. This part of the process is known as the ‘dry end.’
This entire process, from one end of the conveyor to the other, takes up as much length as a football pitch and it all happens extremely fast, with the paper fibre moving along through the conveyor at speeds of up to 2,000 metres per minute.
Paper mills require a very great deal of water to operate, which is why they are almost always located adjacent to a large source of fresh water, like a river. The water needed for the paper-making process must also be very clean and so filtering the water supply of impurities is an important part of the process. Nearly all of this water is recycled and returned to its source and, because of the highly efficient filtering process which the water must go through, the water returned at the end of the process is usually cleaner than it originally was.
Types of boxes
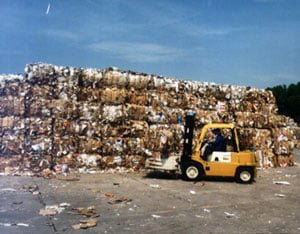
There are many different kinds of boxes, of course, but we will consider two main categories, determined by the type of paper board used in their construction.
Corrugated Cases. Because of their strength, corrugated cases are the most common means of shipping goods from point of manufacture to point of sale. They are ordinarily used for shipping and storing sets of goods of the same size and shape and generally these individual goods are further contained inside other types of packaging, for example, the carton.
Cartons. Cartons are the type of packaging in which goods typically reach the consumer. For example, a breakfast cereal box is a type of carton and many of these cartons would have been shipped to the supermarket inside a corrugated case. Cartons do not need to be as strong as corrugated cases, as they have nearly reached their final destination when they are encountered by the consumer. They do still need to contain and protect their contents, but they also have the function of helping to sell the product they contain by being attractively printed and finished. Printed cartons also display valuable information: content and marketing details, weights and measures, details of the product’s origin and bar-coded information for pricing and stocking purposes.
Cartons are often primary packaging, i.e. packaging which reaches the consumer directly. Secondary and tertiary packaging would include, for example, the corrugated cases in which the products were shipped and other types of packaging not directly encountered by the consumer.
Making corrugated board
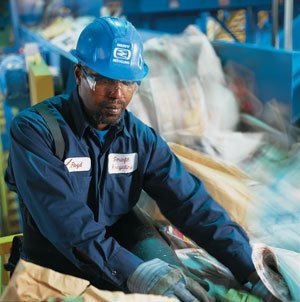
Over 56 percent of the packaging used in the U.K. is made from corrugated board. The great virtue of corrugated board is its strength-to-weight ratio. Corrugated board is made of at least three layers of paper, assembled in such a way as to make their overall strength much greater than that of their individual layers. The technique involves corrugating or fluting the middle layer into a series of arches which give the finished board considerable rigidity. Different types and strengths of corrugated board may be constructed by varying the number of layers – called single, double or triple wall – and also the size of the internal arches. The paper used in the manufacture of corrugated board is an extremely sturdy grade of paper called liner board which is measured in terms of weight (gsm). The main types of liner board are kraft liner (made principally from virgin wood pulp, with smaller percentages of recycled fibre) and test liner (made from 100% recycled paper). The reels of paper are fed into a corrugator, which uses steam and starch to mould the paper into its fluted shape. After this, the outer layers are glued to the fluting and the finished board is cut into lengths and stacked. To produce corrugated cases, this finished board is processed through a machine called a converter, which cuts, shapes and glues the board into its final box form following the customer’s specifications. Corrugated cases are generally delivered flat to the customer.
Because cartons tend to be manufactured for a specific product and because the carton has an important role to play in grabbing the consumer’s attention and selling the product it contains, the first stage in the production of a carton is a consultation between the customer and the carton designer. The size and shape of the carton is determined through the use of CAD systems. A graphic artist using a CAG system will then produce a design for the colours, typography and illustration which will appear on the finished carton. This design will be separated into its constituent colours and rendered on film, from which printing plates will be prepared.
The carton board is fully printed first and then the shape of the carton is cut out, folded and glued. Cartons are also delivered flat and are assembled, either by machine or by hand, at the point where the product is inserted into the carton.
Adding value
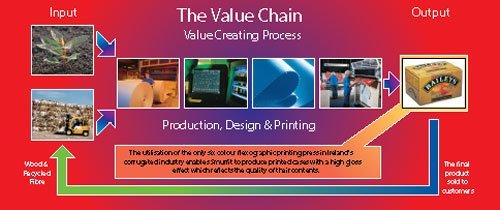
You will have noticed that in every step of the entire process outlined above – from waste paper collection and recycling and the timber forest, all the way through to the box which reaches the final consumer – value is constantly being added to input materials. When timber and waste paper are pulped, value is added. When this pulp is converted into paper, more value is added. Likewise, as the paper is converted into board, the board into corrugated cases and cartons, value is added to what came before at each and every step.
The value chain doesn’t stop there, however, because the business of producing corrugated cases and cartons is a business based on recycling. When the consumer is finished with the carton, the carton becomes waste material which is needed at the very beginning of the value chain – to produce more boxes.
Supply and demand
Because more than half the cost of producing a box is the expense of the paper involved and because the raw materials used in the manufacture of paper are traded globally, global market conditions influence more than 50 percent of the cost of box manufacture. When there is too much capacity in the industry – too many suppliers producing more paper products than the market requires – prices fall. On the other hand, rising demand – which stretches production capacity – will cause prices to increase. Rising demand, however, is usually good news, because the demand for packaging is a good indicator of how the world economy is faring. Manufacturers of goods need more cases and cartons when their businesses are expanding, and so if demand for packaging is up, this indicates that the economy in general is doing well.
Conclusion
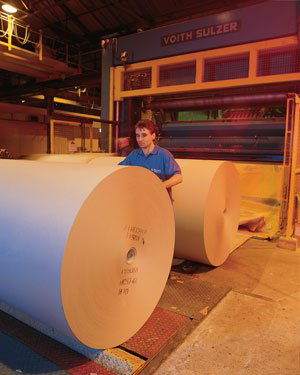
New and more efficient ways of manufacturing paper, corrugated packaging and cartons are constantly being sought – to serve the customer and the consumer better, as well as to protect and preserve natural resources. For this reason, the Jefferson Smurfit Group operates two dedicated research and development centres in Talence, France and Carol Stream in Chicago. These centres are responsible for continual improvements in the processes and products produced by Smurfit companies around the world. Another centre at Epernay, France, is responsible for performance testing of all Smurfit packaging products, subjecting them to simulated conditions of stress and environment which they will encounter when in use.