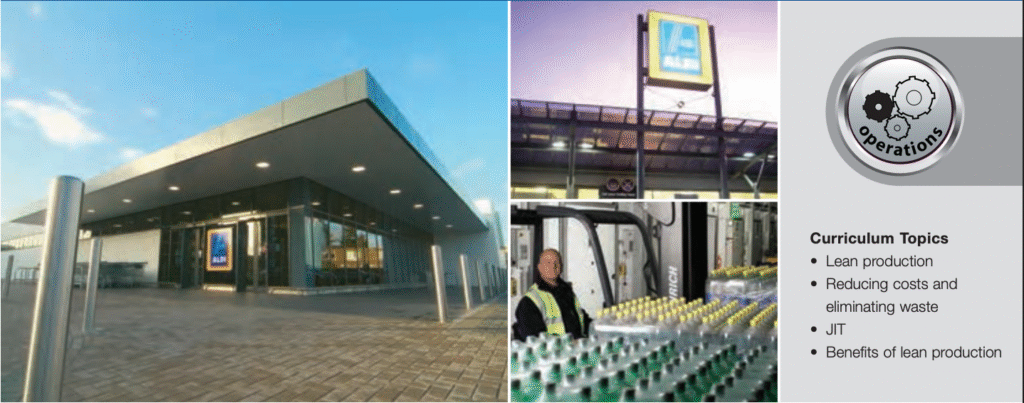
The food retail industry is a highly competitive market. More so than ever, organisations need to offer customers value for money. Customers want the best quality products at the lowest possible prices. With such tough competition, it is vital for organisations to understand what their customers want. Aldi understands that its customers want value for money but do not want to compromise on quality. This case study will demonstrate how Aldi uses a lean approach to its business operations to offer its customers quality products at competitive prices.
Since opening its first store in 1913, Aldi has established itself as a reputable retailer operating in international markets including Germany, Australia and the U.S. Aldi has over 7,000 stores worldwide. What distinguishes Aldi from its competitors is its competitive pricing strategy without reducing the quality of its products. In fact, in some cases, Aldi’s products are 30% cheaper than those offered by its competitors. Aldi can do this because the business operates so efficiently.
Efficiency is the relationship between inputs and corresponding outputs. For Aldi operating efficiently involves reducing costs in all areas of the business. Some of the key areas where Aldi is able to minimise costs are by saving time, space, effort and energy. Aldi’s approach to doing this is to run its business around the principles of lean thinking.
Aldi has a no-nonsense approach to running its business. Whereas other food retailers have elaborate displays, additional services and promotions that draw customers into the business, Aldi’s core purpose is to ‘provide value and quality to our customers by being fair and efficient in all we do’. Everything Aldi does is focused on giving its customers value for money.
Through being efficient and cutting costs Aldi can then invest profits back into the business. They can then be used to further meet its business objectives for growth. Efficiency is not something that is achieved overnight. Lean thinking is a continuous process that constantly enables Aldi to improve the way in which it meets its business objectives. This enables Aldi to develop an ambitious investment programme to develop new properties and suppliers as well as to provide benefits for employees.
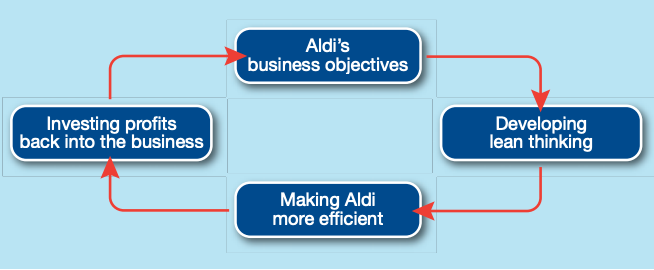
Lean production
Lean production is quite simply about getting more from less. The aim of lean production is to reduce the number of resources used in providing goods and services for consumers. At the same time, it is about making the organisation more efficient. Lean production involves eliminating waste and therefore using less labour, materials, space and time. This in turn reduces costs.

However, for Aldi, lean production is not just about reducing costs for the business. It is also about passing these savings on to its customers to offer value for money. Lean production is based on a number of efficiency concepts, such as:
- Continuous improvement – a culture whereby all employees are constantly involved in making improvements to the quality
- Just-in-time production – materials are received just as they are needed, eliminating the need to maintain large stock levels
- Time based management – an approach that aims to reduce the time wasted in business operations. This usually requires a multi-skilled and flexible workforce.
- Total quality management (TQM) – a quality assurance ideal where all workers have a responsibility for getting it ‘right first time’
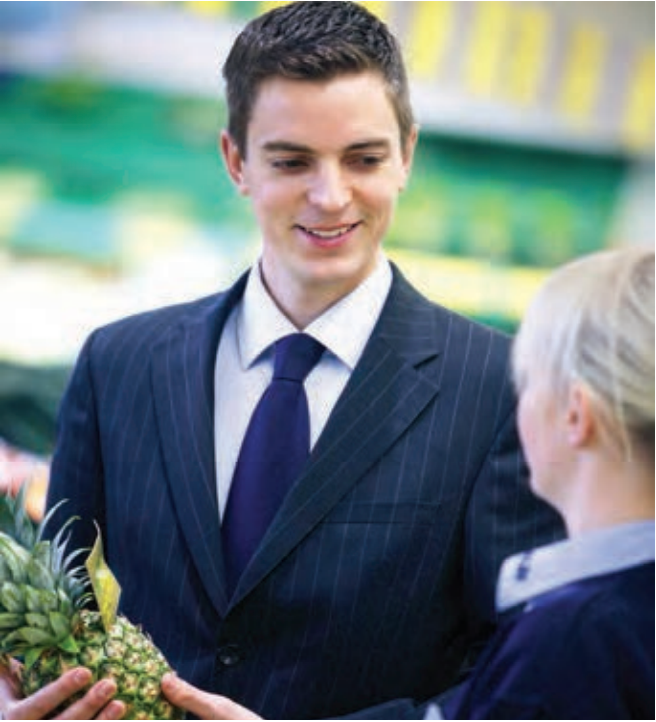
Principles of lean production
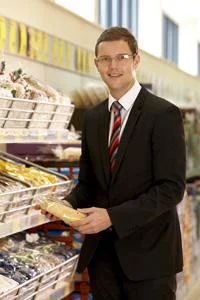
Although lean production is often considered in terms of manufacturing, these principles can equally be applied to service organisations. The principles of lean production are planned and built into everything that Aldi does. This starts within its supply chain. For example, up to 60% of Aldi’s fruit and vegetables are sourced locally where possible, reducing the need for long and costly delivery journeys. This demonstrates a time based management approach.
The principles of time based management are also built into the training provided for Aldi’s employees. Training enables Aldi to eliminate waste and cut costs. By training staff to do a variety of tasks around the store Aldi can minimise its staff requirements. This method results in staff gaining knowledge of the whole business, as such they are able to offer a much higher level of customer service. Staff costs can also be reduced as fewer staff are required if they can perform a variety of duties throughout the store.
Aldi also applies this time based management approach to its product range. For example, Aldi sells fewer variations of each product. In contrast, competitors may sell a larger variety of different brands, sizes and packaging. By selling fewer varieties of each product Aldi can buy much larger quantities. This enables it to take advantage of economies of scale and source products more cost effectively. This in turn means that Aldi needs less space to display its products. As a result, Aldi’s stores can be smaller.
The three core values of Aldi are simplicity, consistency and responsibility. Lean production ties in closely with these values. For example, Aldi stores are simple in design and all stores are very similar which creates consistency.
Responsibility is an important aspect of all areas of the business, from training and developing employees to drive the business forward as part of continuous improvement, to taking an active role in its supply chain to ensure continuous improvement. Such actions have helped it to develop an international influence in different markets.
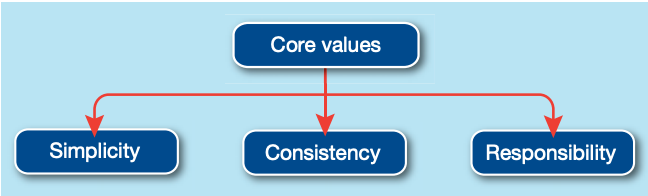
Reducing costs and eliminating waste
Lean principles involve minimising waste. Aldi has adopted a number of different time-based management approaches to ensure that waste is kept to a minimum. Minimising waste can help reduce costs. For example:
- Aldi’s shopping trolleys have a £1 deposit system. This ensures that customers return them after use. This results in fewer trolleys being lost and needing replacing. It also means that Aldi does not have to employ someone to collect the trolleys as customers return their trolleys to the front of the store.
- Another time based management approach that Aldi has adopted to reduce waste is through its opening hours. Aldi trades from 8 am until 8 pm from Monday to Saturday and from 10 am until 4 pm on Sunday. In contrast, some of Aldi’s competitors are open 24 hours. This means Aldi’s sales are spread over a shorter period. It also means that staffing costs are not incurred at times when there would be fewer customers. As a result, Aldi is more productive during its trading hours. Consumption of utilities for power and heating can also be reduced through trading only during the busiest times of the day.
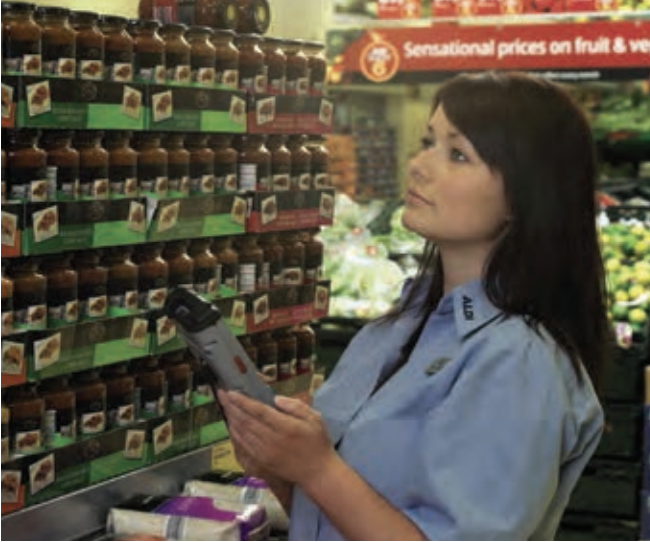
To underpin these principles Aldi requires competent staff. A combination of total quality management techniques and a time based management approach help to ensure employees take responsibility for their job roles whilst minimising the amount of time wasted. Employees are paid market-leading salaries within the grocery industry.
A comprehensive training programme enables them to become multi-skilled. This means that staff can undertake a number of different roles within each Aldi store, allowing staff to be flexible with the tasks they can do. It is therefore easy to produce a staff rota as employees can fulfil a variety of tasks. Employees can carry out whatever tasks are needed throughout the day, leading to time-based savings. Training, high wages and diverse job roles all help to motivate staff. This in turn leads to lower sickness levels and a more empowered team.
The process of buying and selling within Aldi stores also operates on time-based management principles which means that they require fewer tills and cashiers. For example:
- Products display numerous bar codes. This means that cashiers do not have to search for them and they can be scanned more quickly.
- Customers place products back in the trolley after scanning. They then pack their bags away from the till after paying. This helps throughput. It is also more efficient as another customer can have their shopping scanned as the previous customer packs. Again, these cost benefits can be passed on to customers.
These processes contribute to savings which help Aldi to operate more efficiently as an organisation. The savings are then passed on to its customers. This is in the form of quality products at prices that are lower than the competitors.
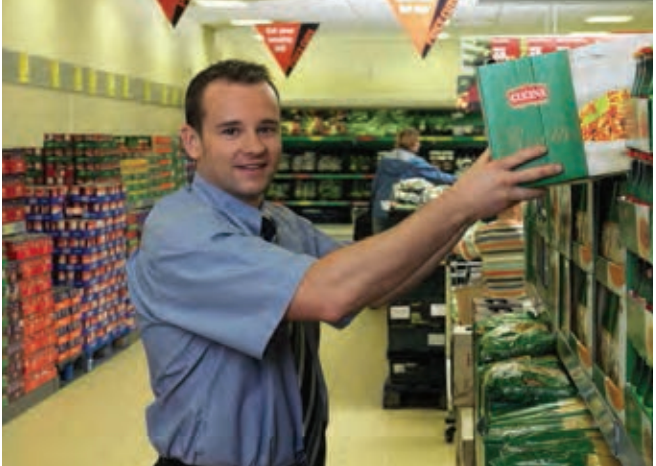
JIT
Aldi uses a just-in-time (JIT) approach to store management by only holding the stock that it needs. Stock is expensive. The company therefore only buys the stock required at any given time. When stock levels are reduced an organisation’s working capital is improved. In other words, Aldi is not tying up too much investment in a stock that is then going to be held for a long period of time before it is sold to generate income. It also means Aldi does not pay for large warehouses to store stock or pay for additional staff to monitor warehouse stock.

From the moment stock arrives at an Aldi store, everything is focused on reducing the cost of holding and managing the stock. For example, products are delivered in display ready cases. Once the top of the case is removed it can simply be lifted onto a shelf for a display to customers. Units of 12, 24 or more can be handled easily and quickly merchandised. It means that individual units are not picked and lined up on shelves. In fact, some products are sold in store from a pallet. This is a platform for large loads that can be brought mechanically into a store. This is an efficient way of getting a large volume of products into the shop very quickly.
Benefits of lean production
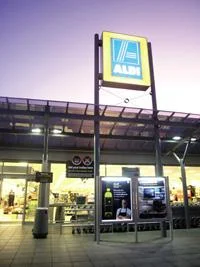
Aldi’s ‘no-nonsense’ approach to retailing therefore leads to cost savings in numerous areas. These cost savings are passed on to customers in the form of lower prices, allowing the business to differentiate itself from its competitors in terms of price, as well as the quality of the products it has on offer. Also, as money is not wasted on unnecessary expenses, Aldi is able to allocate spending to other important elements of its business. For example, Aldi is also focused on corporate social responsibility(CSR). These are Aldi’s wider responsibilities to society, its employees and the community. Aldi also works with many different charities. For example, in 2011 Barnardo’s was Aldi’s charity of the year.
Through using a total quality management approach, Aldi is able to create strong business relationships with its suppliers. These strong relationships help Aldi to continuously improve its product offering whilst also ensuring suppliers meet international standards. Aldi’s international standards go beyond consumer legislation and nutritional information. Products are carefully labelled for consumers so they can make informed choices, this all supports Aldi’s continuous improvement culture.
Conclusion
Aldi has a distinctive approach to retailing. Its operations focus on providing its customers with quality products that are value for money. Aldi achieves this by ensuring that its operations are as efficient as possible whilst also adhering to its core values of simplicity, consistency and responsibility. Through adopting a variety of lean approaches Aldi is able to offer its customers the highest quality products at the lowest possible price.