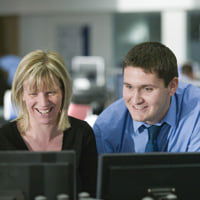
Planning a major project is an exciting and challenging activity. This case study focuses on the planning that went into repairing Network Rail’s Leven Viaduct situated in Cumbria. Any major engineering project requires planning for:
- the activities that need to be completed
- the sequencing of these activities
- the timing of the start and completion of these activities
- budgeting of costs involved.
Built in 1857, the Leven Viaduct on the Cumbrian coast has been a vital rail link between the North and South. At almost 500 metres long the viaduct was a major engineering project when first built. Even today its reconstruction presented Network Rail with a huge challenge. Through careful planning the project was completed in 16 weeks half the time originally anticipated.
Decision making
The project was required because heavy seas, corrosive salt water and heavy use meant that the viaduct was wearing out and would become unsafe. There were two main options:
1. repair the viaduct
2. close down the line and re-route all traffic on to an alternative line.
At the heart of the decision-making was the need to look at the costs of the two alternatives.
- Option 1 was costly estimated at £20 million, plus the ongoing cost of maintaining the line.
- Option 2 would however overload the West Coast main line. This would lead to delays on a very important route from Glasgow to London.
It therefore made sense to repair the viaduct.
Operations planning
A plan of operations is required to see a project through from start to finish.
Objectives
An important starting point is to set out your objectives so that you know where you are going. Key objectives for the Leven Viaduct project were to develop and implement a solution that would:
- require no major maintenance for 25 years
- remove any risk of line closure due to structural problems.
Engineers had to work out what was possible within a given budget and time constraints. For example, they had to consider the types of materials and fittings to use. They had to liaise with users of the rail line. This involved discussions with passengers and with companies which used the line to send freight. It also involved talking to the local community and environmental groups. A number of key issues and risks had to be considered in creating plans, such as delays. Resulting from bad weather and environmental considerations.
Critical success factors
In creating the plan a number of critical success factors were identified. These were:
- to deliver the project within a given budget
- to have no accidents or incidents during viaduct construction
- to establish good relationships with the community and to respect the local environment
- to ensure the efficient procurement of the steel that was essential to the project to minimise disruption to passengers and freight.
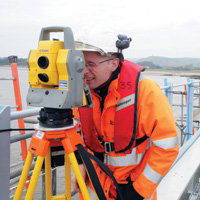
If Network Rail did not achieve one or more of these factors, it could have resulted in negative publicity and cost in production time or even legal action. The project involved huge tasks. The existing brickwork of the piers, or columns, which support the viaduct had to be repaired. The existing rails and decking needed to be taken up and replaced. This was a £14 million investment requiring:
- the use of 3,500 tonnes of steelwork – this took nearly six months to produce
- the replacement of 1,100 metres of track – if all the steel units and rails were laid end-to-end, it would stretch for nearly five kilometres
- 2,000 m2 of brickwork repairs to the piers – similar to the size of a football pitch.
Roles within the organisation
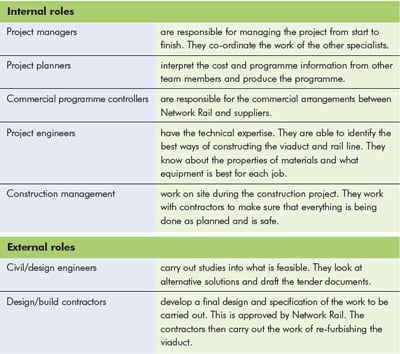
Network Rail owns and operates Britain’s rail infrastructure. The company strives to provide Britain with a safe, reliable and efficient railway fit for the 21st century.
The company provides an excellent career structure with interesting work as shown by the Leven Viaduct project. A number of different roles were involved in planning and carrying out the project. Some of these were internal to Network Rail. Other roles involved bringing in external specialists.
Co-ordinating people via Critical Path Analysis
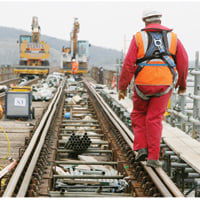
Major construction projects involve a lot of separate steps. For example, in constructing the viaduct, the 96 pre-fabricated metal decks which made up the main structure of the viaduct were specially made off-site and transported by rail from Ulverston.
Some activities in a project can be carried out simultaneously – for example, while the metal decks were being made, the piers supporting the viaduct were repaired at the same time. Other activities need to be carried out in a sequence, for example, you can’t lay the new rail track before the old track has been taken up. We say such activities are ‘dependent’ upon the completion of the previous one.
Critical Path Analysis
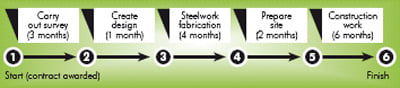
Critical Path Analysis involves setting out a diagram showing all of the activities involved in a particular project and how they relate to each other. The following network diagram shows the main sequence of activities involved in carrying out the project.
The process
It would be too complicated to show all of the steps in the construction of the viaduct because there were so many operations involved. However, the process can be illustrated by taking an example of part of the process.
In order to simplify this we shall assume that:
A – This part of the process starts with the fabrication of the steel which is expected to take four months.
B – This is followed by site preparation which takes two months. This is dependent upon activity A.
C & D – After site preparation, the walkways can be built (two months) followed by the decks (two months). Activity C is dependent upon activity B and activity D is dependent upon activity C.
E – While the walkways and decks are being built the piers can be repaired (which is expected to take five months). This means that activity E is dependent upon activities A and B.
The network diagram
This is illustrated in a new network diagram:
- The circles in the diagram are called nodes. They show the start or finish of a task. The nodes are split into three sections. In the left hand semi-circle the node number is written.
- The number in the top right is the earliest starting time (EST). This shows the earliest time the next activity can start.
- The number on the bottom right is the latest finishing time (LFT). This is the latest that the previous task can finish without delaying the next task. Arrows show the order in which activities take place.
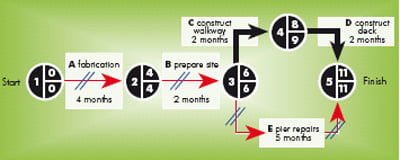
For example, in the diagram the earliest activity B (preparing the site) can take place is after 4 months, when the steel is ready. The earliest that pier repairs can start is after 6 months, when the site is prepared, etc.
The critical path
The next step is to set out the critical path. Critical activities are those which most urgently need to be completed on time to ensure the whole project is not delayed. For example, if the pre-fabricated steel did not arrive on time then this would be a serious problem. This shows how important the role of a good Project Manager is. We can illustrate the critical path by highlighting it in red through the arrows on the diagram. This joins up the sequence of activities that will take the longest. The critical path can also be indicated by drawing two parallel lines (shown in blue) across the arrows between nodes. In this case the critical path is through the activities A, B and E. This is because E takes five months whereas C and D together are only expected to take four months. Site managers and contractors must pay particular attention to E (pier repairs) if the whole project is not to fall behind schedule.
Network Rail’s Leven Viaduct engineers were dealing with a project which involved hundreds of separate processes. They used spreadsheets and computer models to give them a detailed picture of all of the stages involved. Every day they kept a close eye on where the project had got to. This enabled them to put in extra resources whenever there was a delay, particularly along the critical path.
Advantages and disadvantages of Critical Path Analysis
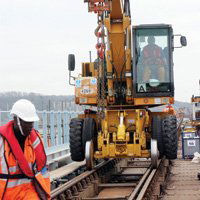
Critical Path Analysis is a very useful tool for Project Managers. It helps them to focus on the key activities of a project and how they all fit together. Project Managers and site managers can then allocate resources to critical activities. These are ones that require extra consideration to make sure that everything runs smoothly.
Monitoring the process
The Leven Viaduct planners created a spreadsheet which identified the budgeted costs of each of the steps involved in their project. As a result they were aware at all times of the cost implications of each stage of the project, and the importance of getting each step in the sequence finished on time. Delays can add extra costs to a project and can involve financial penalties for being late.
Benefits of Critical Path Analysis
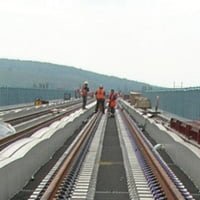
Critical Path Analysis is a very detailed process. However, the time spent in putting the plan together was well worth it. Careful planning meant the project ran smoothly which led to cost and time savings later on. At the same time, Network Rail was able to take on board the highest safety standards and consideration for the environment. Of course, carrying out such an analysis does not guarantee success but it certainly helps. Creating the plan enabled the engineers to identify improvements to ensure the project finished on time. For example, at an early planning stage, they increased the number of construction workers required.
Conclusion
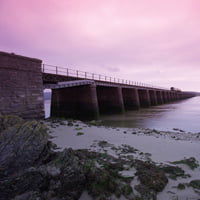
The Leven Viaduct project provides a good example of the challenges and excitement of working for Network Rail. On 16th July 2006, the viaduct was officially re-opened on time and to budget. Network Rail invested £14 million to remove decking and support girders across all 49 spans of the viaduct, improving safety standards and guaranteeing the availability of a vital transport link. In doing so they were able to secure the future of one of the North West’s most historic and impressive landmarks for another 140 years.