BSI was the pioneer in creating standards. It is the UK’s National Standards Body – the world’s first. It also plays a prominent role in the development of global standards. BSI:
- leads in the creation of standards
- tests and certifies products and services
- is one of the organizations that assesses Quality Management Systems (QMS).
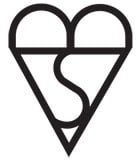
Businesses gain an advantage over rivals and also gain a high reputation by producing high quality goods and services. Using standards helps businesses to do this. The standards are based on best practice – for example, in handling environmental waste or storing data.

BSI provides certificates such as the Kitemark. The Kitemark shows that a product or service conforms to rigorous standards for safety and performance and has been tested against them. It is a trusted symbol found on objects people can take for granted every day, such as electrical plugs and double glazed windows. It is also on objects we all rely on in an emergency, e.g. fire extinguishers and surgeons’ gloves.

BSI works with all types of organisations. The table shows a breakdown of companies, by sector, that are licenced by BSI as a result of meeting the international standard for Quality Management Systems (QMS) (ISO 9001).
This case study focuses on the benefits of quality and how an organization designs and implements a quality system.
What is quality?
Quality is defined by the customer. A quality product or service is one that meets customer requirements. Not all customers have the same requirements so two contrasting products may both be seen as quality products by their users.
For example, one house-owner may be happy with a standard light bulb – they would see this as a quality product. Another customer may want an energy efficient light bulb with a longer life expectancy – this would be their view of quality. Quality can therefore be defined as being fit for the customer’s purpose.

There are three main ways in which a business can create quality:
Market research
Market research involves a business in finding out what its customers want and expect. It can be carried out with a small group of customers, asking them to provide detailed information about products and services. The research should reveal what the customer’ view of quality is and whether they are getting it. Obtaining lots of information from a small panel of customers is a way of obtaining qualitative research.
Market research can also be carried out with large numbers of customers through questionnaires. This may provide quantitative research.
Best practice
Working to best practice standards is another way an organization can create quality. BSI works with industry specialists to create these standards. For example, it delivers the confidence of customers in a business through BS 7799. This is the standard for a company’s management of information security.
BSI developed this standard in 1995 to establish best practice for capturing, storing and handling data. This British Standard became the basis for the International Standard ISO/IEC17799. Today companies worldwide are seeking certification for their security management systems.
Why is quality important?

The most successful organizations are those that give customers what they want. Satisfied customers are loyal to those suppliers they feel best understand their requirements. As a result they will make repeat purchases and will recommend a business to their friends.
There are two main types of customers for a business:
- end customers – people like you and me, looking to buy an iPod or plasma screen television
- organizational customers – for example, a company recording audio CDs would buy in blank CDs, record music to them and sell them on as a finished product.
When you buy a piece of electrical equipment, you will want to know a lot of information about its specification. Obvious information that you will be looking for include:
- Is it safe?
- Does it do what I want?
- Does it meet the required standards?
As a customer you will have a lot more confidence in products you know have been tested and meet British, European and International Standards. In the same way, your school will want to purchase gym and science lab equipment that meets the specifications of the safety standards.
Businesses therefore benefit from working with BSI to meet standards, because:
- Standards protect consumers’ fundamental right to safety, the right to be informed and the right to choose. These rights relate to products, services, processes and materials.
- Standardization promotes effective research and development, and makes products easier to use.
- Standardization relies on all sections of society being involved in standards, providing an opportunity for everyone to share knowledge and make their voice heard.
- Businesses that do not focus on quality will quickly find that there are costs to be paid. Examples of these costs include waste due to products being badly made and therefore not being able to sell them. The reputation of a business will quickly deteriorate as a result of poor quality work.
It is very important for UK businesses to be associated with quality. Today, there is greater competition from abroad.
Standards are continually changing so it is important for businesses to keep up. For example, ISO 9001 which is outlined in Section 4, started out originally as a British Standard, BS 5750 in 1979. It was developed as an international standard and became known as ISO 9001 in 1987. Today, the latest edition (2000) has been adopted by more than 400,000 organizations across the globe.
Implementing a quality system – internal
Quality management systems
A system is a group of interrelated parts that make up a whole. A quality system therefore consists of parts (such as policies and processes) designed to ensure quality.
A variety of organizations work with BSI to create standards for QMS. The standard specifies requirements for a QMS where an organization:
i. needs to show that it can consistently provide products that:
- meet customer requirements
- meet any legal requirements.
ii. aims to improve customer satisfaction as a result of applying the system. This includes continually improving the system.

ISO 9001 sets out eight quality management principles. These include:
- customer focus
- leadership – a commitment to quality by the leaders of the organization
- involvement of people – everyone in the organization having a part to play
- making sure that those processes which create quality are identified
- continual improvement of the system.
In practical terms, organizations wishing to apply QMS take the following steps:
- Read and understand the standard. They read through the literature and discuss any issues with BSI.
- Use supporting literature and software tools to help understand, develop and implement QMS.
- Involve top management (heavily) in developing a quality management plan. Typically a Quality Manager will be responsible for the initiative.
- The Quality Manager can be trained in ways of implementing the standard.
- The QMS is then created and put into practice.
- When the organization feels confident it is meeting the standard, it informs an assessor, who will assess the effectiveness of the QMS. If it meets the standard a certificate will be awarded. This is subject to regular reviews.
Implementing a quality system – external
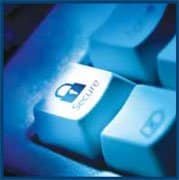
Internal systems are ones that are built inside an organization. However, in addition, modern businesses need to build external systems. External systems are those that involve people outside the organization – e.g. suppliers.
Today, many businesses have long supply chains in which they source materials, parts and finished goods from across the globe. Take, for example, a modern plasma screen television. Some of the components may come from India, others from China, or Eastern European countries. These separate components will then be assembled into a sub-assembly i.e. part of the finished television. This sub-assembly may take place in India, whilst a number of parts may then be transported and delivered to a final assembly plant in Wales.
This has led to a change in attitude. Instead of a company having a ‘them’ and ‘us’ attitude – where ‘them’ are the suppliers, it now makes sense to see the process as a shared one in which everyone relies on each other. This is known as interdependence.
Conclusion

In world trade, for buyers and sellers to work together there must be trust. Standards can provide the necessary bridge of confidence and understanding that builds mutual trust, helping trade to thrive.
Sales are the lifeblood of any business, so the implementation of standards helps sales. This is the case whatever the size of the business or the sector they are operating in.
Following are case study samples of the implementation of quality:
JC Garland & Co – Case study on quality
Garlands is a leading UK provider of outsourced customer contact services. Its services range from customer service to debt collection, customer retention, technical assistance, cross-selling, staff accounts, credit management, customer registrations and many other back office functions. The company owns five prestigious contact centres, and is the second largest private sector employee in the Tees Valley with over 3,000 staff.
Prior to implementing a quality management system, the policies and procedures used originated from a variety of sources. Some met specific needs – e.g. legal requirements for Taxation, Accountancy, Health & Safety and Employment – some had evolved over time, while others were adopted to service specific client requirements.
As a growing number of organizations required their suppliers to be ‘Quality Registered’ management decided to pursue ISO 9001:2000 accreditation. It saw clear benefits in accreditation – but were keen not lose the company’s strong corporate identity.
All company procedures and processes were extensively reviewed internally and a formal Quality Management System (called Everest) was established to comply with the requirements of the standard.
BSI undertook pre-assessment audits. Garlands gauged the effectiveness of the system and determined what improvements were needed. In February 2005, a formal accreditation audit was undertaken and Garlands was recommended for registration.
After receiving the formal registration certificate Chey Garland, Chief Executive of Garlands Call Centres, said
“Gaining ISO 9001:2000 certification isn’t just nice to have, it’s vital to the success of our business. It will enable us to expand in important sectors such as financial services and Government, where organisations frequently require proof that their business partners can adhere to tough quality standards. It will open up significant new business opportunities.”
On-going internal audits and regular BSI continuous assessment visits ensure that Garlands maintains high standards, continues to conduct best practice and is able to establish areas of continual improvement.
MC Fire Protection Ltd – Case study on quality
Companies offering fire risk assessments and consultancy services use these as industry standards. By obtaining ISO 9001 registration they are able to show that the whole service offered is professional and high quality. One such company is MC Fire Protection.
MC Fire Protection was established by Mike Chilman, and has earned an impressive reputation whilst working within the fire industry based in Bicester, Oxfordshire. It employs a team responsible for covering the supply, installation and maintenance of Fire Extinguishers and Fire Alarm Systems, together with a consultancy service covering all aspects of fire risk management. New contracts are currently being driven by Insurance companies and changes in European and British legislation, which are partially responsible for increasing sales.
Businesses are legally required to take steps to protect themselves, staff and customers from dangers like fire. Fire protection often relies on equipment like fire extinguishers and alarms. These have to comply with the fire safety standards. This provides the reassurance that the equipment will do its job.
Mike Chilman, MD, explains why:
‘In 2004, our competitors were starting to publicise the fact that they complied with it. A lot of businesses choose to trade with companies that comply with recognized standards ahead of those who don’t. On a practical level ISO 9001 has made positive changes with improvements to our workshop, supply chain and record-keeping. All the standards we apply have brought us extra reassurance. They help us to show that we’re more professional, while our customers are assured that the services we provide are high quality. I would recommend standards to other businesses in the fire-protection industry – in fact, it’s becoming more and more of a necessity’.