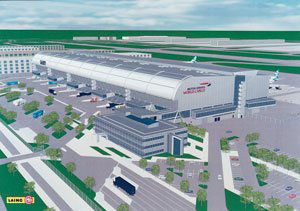
One of the most significant economic developments is the internationalisation and globalisation of commerce. Almost every type of business is influenced by global events – businesses now face tough competition in home markets from overseas producers, but benefit from new sources of products, parts and goods which have become available. Companies today have extended their geographical markets as well as the areas in which they purchase and manufacture – creating a much more complex and competitive business environment at a time of rapid growth in world trade.
In order to achieve customer satisfaction, businesses must ensure that products and services are available for customers as promised, at the right time and in the right place. Businesses must operate a range of innovative manufacturing concepts, such as just-in-time production, which affects how successfully they cater for their customers. Just-in-time means that production materials arrive at a customer’s factory exactly as they are needed for production, thus avoiding costs of storing materials until they are used. It calls for close coordination between the supplier and the customer, as well as an efficient distribution system. Logistics is a key element in guiding the planning and development of many businesses. High standards of logistics, for example, might allow a supplier to deliver 99% of customer orders within 48 hours of the order receipt – helping that company to win new customers and retain existing ones.
A key industry which has grown rapidly in recent years is that of Air Cargo. The industry has been supported in its response to the process of change with state-of-the-art technology and some of the latest engineering concepts in the world.
This case study focuses upon a pan-European project which involves GEC ALSTHOM and Lödige who are currently developing a Materials Handling System for British Airways at its New World Cargocentre at London Heathrow Airport.
Objectives and strategy
Early in 1994, British Airways World Cargo appointed WS Atkins as Design Consultants for the New World Cargocentre at London Heathrow. The strategic brief established the design mission as:
- The objective. To provide the built infrastructure and physical tools to support the most successful air freight carrier in the world.
- The means. To create a pattern making design which will set a new benchmark for the industry.
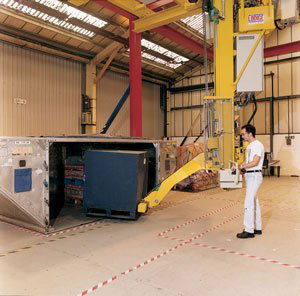
The underlying philosophy behind the Cargocentre was that British Airways World Cargo would provide a seamless link in the supply chain for manufacturers, distributors and producers with the Cargocentre benchmarking its processes against the best, not only in air cargo, but in areas of high tech manufacturing. The Concept Design report was completed in July 1994 with a final design for the Cargo Freight Centre for a building 300m long x 95m wide x 37m high. The Scheme Design for the Materials Handling System was started in July 1994 with Lödige Industries of Germany as designers and WS Atkins Consultants acting as the design coordinator. A good logistics system aims to provide the best possible service at the lowest possible cost. To fulfil British Airway’s corporate objectives, the New World Cargocentre needed to:
- provide a seamless service to the customer
- fulfil customer service targets for the different cargo products
- support maximum revenue for British Airways
- minimise costs at each stage of the handling process.
The basis for design, in terms of the cargo to be handled, was a minimum capacity of 800,000 tonnes per annum with a maximum capacity of 1,000,000 tonnes per annum. There were many other key requirements for the Materials Handling System. For example, it was important to have an improved and safe working environment for staff. There was to be no physical differentiation between import and export goods, although a logical separation should remain for Customs’ purposes. Maximum usage should be made of the building volume with the holding of cargo on the floor minimised and the system control needed to interact with other British Airways systems.
The Materials Handling System needed to provide a cost effective solution to British Airways World Cargo requirements in which it would be possible to identify the location of every item of cargo in the system. The design was completed by late 1994 and during early 1995, British Airways World Cargo was ready to issue the tender for the provision of this system.
Setting up a pan European project
Before the issue of the Materials Handling System tender, GEC ALSTHOM held discussions with Lödige Industries, on the basis that the products and experience of the respective companies were complementary.
GEC ALSTHOM is a world leader in Power Generation, Transmission & Distribution and Rail Transport. It has a significant presence in Industrial Automation. GEC ALSTHOM’s Engineering Systems business specialises in baggage handling and automated warehousing systems and therefore possessed the necessary expertise relating to the handling and storage of consignments to and from the Unit Load Devices. (Unit Load Devices – ULDs is the general term for the special cargo and baggage carrying devices which fit into aircraft, ranging from flat pallet boards to shaped containers.)
Lödige Industries has a world-wide reputation for the design and implementation of large fully automated air cargo handling systems, including Unit Load Device handling. The company has maintained a leading edge by investing in product development and dedicating its engineering team to the task of meeting the future needs of the industry.
The potential existed for these two leading organisations to combine their efforts to secure the British Airways contract. During the first half of 1995, a Consortium was formed with GEC ALSTHOM as the Lead Contractor and in August of that year, the contract for the Materials Handling System was won at a value of £87 million. The project has now become truly international with subcontract projects granted to companies in Denmark, Holland and France, as well as many components coming from other European sources. The New World Cargocentre is due to be completed by January 1999. It is British Airways’ largest non aircraft investment.
Project management
It was recognised at the outset that the two companies, GEC ALSTHOM and Lödige, would need to form a task force to plan and implement the project. In order to carry out the work successfully, it was vital to have a fully integrated project team which would appear ‘seamless’ not only to the client, but also to those employed in the teams.
Handling process
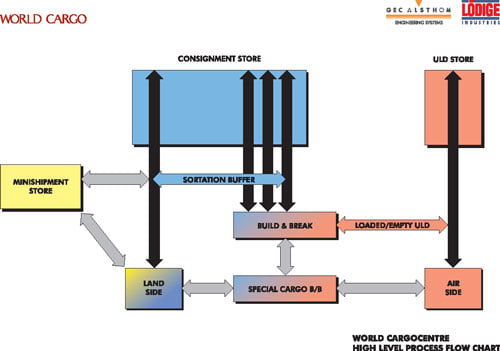
The British Airways World Cargocentre is a purpose-designed, multi-level structure, housing an automated cargo handling system. Each floor of the Cargocentre has a specific function.
The ground floor level provides the customer interface facilities of lorry docks for delivery and collection of cargo through a number of points. The handling of Unit Load Devices is also at ground level. There are special storage areas here, as well as facilities for loading and unloading Unit Load Devices and facilities for loading and unloading cargo into the consignment cages.
The first floor provides the location for the general Unit Load Device load and unload stations where cargo from the consignment cages is handled by power manipulators or manually to and from the Unit Load Devices. Cages and Unit Load Devices are transported to this area by hoists from the storage areas and from the ground floor.
The second floor houses the cargo sorting equipment – an automatic sorting machine together with transport and storage conveyors to achieve a highly automated sorting system. The sorted packages are routed to consignment cages or to delivery conveyors to customers collecting their packages.
The levels above the second floor are the entirely automated consignment store with lifts for moving goods to and from each level below and transfer vehicles for moving between different parts of the building. The consignment store is located towards the landside of the building and the Unit Load Devices store is towards the airside.
Key features of the operation are:
- total flexibility to intermix imports and exports
- the use of Electronic Data Interchange (EDI) as part of the coordination between flight patterns and lorry/freight forwarder pick up times
- prescheduled work to minimise storage time
- the bar-coding of packages with an interface into British Airways’ inventory management system
- automated storage
- S-2000 sorting system which has a capacity of more than 4500 units per hour
- special cargo handling facilities for hazardous materials.
The materials handling system ties in with all movements to suit air cargo flights and outside traffic patterns. A document handling system is routed around the building to provide a rapid means of sending cargo documents to delivery and collection areas.
Innovation
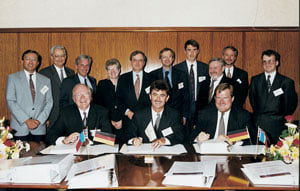
The key to the success of the New World Cargocentre is total flexibility and this has been achieved by a system design that can handle imports and exports as and when required, subject to the requirements of Customs & Excise regulations. This enables the whole system to swing naturally from one activity to another.
Another major innovation is the cargo handling Manipulator, designed and developed by Lödige to act as the ‘mechanical hands’ in the load and unload operation. This is where the cargo is transferred from Unit Load Devices to consignment cages and vice versa. Replacing existing fork lift trucks, these ceiling suspended lifting and carrying devices have the ability to rotate 360° on the spot and move in any direction whilst being extremely responsive to operator control. With the capacity to lift 1000kg with its fully extended arms each manipulator has the sensitivity to pick up a tray of full coffee cups without spilling a drop.
Design process
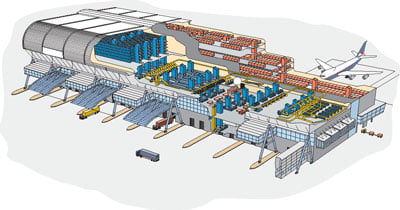
The design of such a large and complex scheme entailed the co-ordination of a large number of people from many disciplines. Experts from mechanical, electrical and electronic engineering, safety, quality, risk management and ergonomics all made important contributions to key elements. Computer aided design (CAD) and simulation was used throughout the design process to show how the performance requirements could be met.
The safety of personnel in construction, operation and maintenance was of paramount importance and was, therefore, taken into account in the design process. The safety and security of cargo was also a critical factor. As this is such a complex undertaking, the supplier cannot work in isolation. There were many meetings with the client and other interested parties to ensure that the development was fully integrated.
The SARM assessment method is concerned with the Safety, Availability, Reliability and Maintainability of the plant and equipment. It aims to improve plant performance in each of these aspects throughout its lifetime. Purchasing at lowest cost does not necessarily deliver the best value for money. The SARM policy focuses the supplier on the through life cost of a project. It is the through life cost which is important for the user and this does not necessarily result from the lowest initial capital costs.
The best investment payback is the optimum balance between capital costs and running costs at the desired level of performance of equipment. In order to make decisions regarding the balance of capital and running costs, a number of performance factors are taken into consideration. For example, as well as the engineering performance, parameters of Rate and Quality or Value, measures of Reliability, Maintainability and Risk need to be established.
The SARM assessment methodology is aimed at the prediction of the functional life time cost and risk parameters of Safety, Reliability, Availability and Maintainability, to optimise the design and minimise the cost of ownership. This concept is applied not only during the design phase of the project but also when the plant comes into operation.
Conclusion
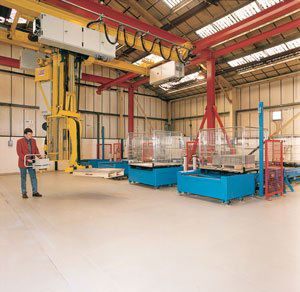
If British Airways World Cargo is to become the most successful air freight carrier in the world, it needs the infrastructure and tools to support its operations. British Airways’ investment has created one of the most sophisticated automated cargo handling systems in the world which puts customer needs first and provides a seamless link in the supply chain. It has created a safe and pleasant environment for both customers and staff and represents a major improvement in efficiency – ensuring the safe and effective handling of customer freight with continuous cargo traceability.
The key driver for the New World Cargocentre is British Airways’ ability to differentiate its products and services. The use of advanced technology process systems, using pan-European experts such as GEC ALSTHOM and Lödige Industries, has successfully created a system with the flexibility required by the airline’s complex operations.