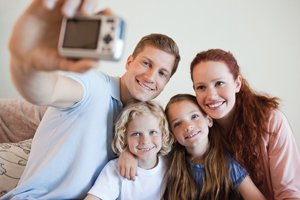
Zurich Insurance Group provides insurance and other financial services to both individuals and businesses. The group has more than 130 years experience and is one of the world’s largest insurance groups. It has more than 60,000 employees and operates in over 170 countries. In the UK alone, Zurich has over two million live policies and each month its Life business handles 300,000 interactions with customers by telephone and mail, as well as a further 300,000 email and internet enquiries.
Zurich products and services include insurance for properties, accidents, cars and life. The aim of insurance is to help people and businesses protect themselves financially if something goes wrong. There can be major financial consequences if expensive assets like buildings and cars are damaged. People need assurance that they will not suffer if someone is unable to work, requires extensive treatment or care because of an accident or dies.
The policy holder has the reassurance that if something goes wrong, the consequences are managed and Zurich’s insurance will, at least financially, help to put things right. In exchange for its customers paying money in regular premiums (over a specified period of time) Zurich promises that it will be there when it is needed.
Code of conduct and core values
In a service industry many companies offer broadly similar products. Quality is one way in which Zurich can differentiate its services from those of its competitors. It puts delivering quality customer service at the heart of everything it does. Zurich’s ambition is to be the best global insurer as measured by its customers, shareholders and employees. Zurich demonstrates its commitment to achieve its ambition through the Zurich Basics; its code of conduct for all employees based around five core values – Integrity, Customer Centricity, Excellence, Sustainable Value Creation and Teamwork.
This case study examines how Zurich brings quality to life in the care it provides for its customers every day.
What is quality?
Quality can be described as ‘fit for purpose’. Note that quality does not necessarily equate to ‘luxury’. For example, if someone wants to hire an economical and easy-to-park car, then a model such as a Smart car would adequately meet the customer’s need so would be fit for purpose. Providing anything of a higher standard would be an unnecessary cost. Quality is linked to what the customer needs and expects. If a product meets these needs and expectations, then it can be considered a quality product.
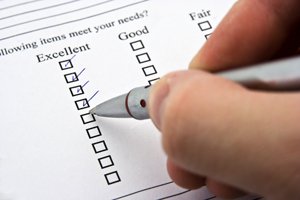
Quality is also linked to the target market of a business. The level of quality required to be fit for purpose is different depending on the types of customers a business deals with. For example, a customer willing to pay £50 per night for a hotel room will have lower expectations than a customer willing to pay £200 per night. However, in both cases, the customer will consider whether the quality of the room is fit for purpose based on the amount they have spent.
Quality is equally relevant to a service business as to a manufacturing one. Zurich must therefore establish what its customers need and expect. It must deliver on its promise to be there when its customers need assistance, efficiently and courteously.
Meeting customer expectations
The ability to meet customer needs and expectations and deliver on its core promise determines how customers feel about the Zurich brand. To ensure that customers have a positive experience, Zurich focuses on:
- clearly identifying customer needs
- effective planning and processes
- putting in place the right resources (people and systems) for the job
- providing in-depth employee training to ensure that all staff are customer focused
- setting appropriate and achievable targets
- continuous measuring and monitoring of progress against these targets.

Zurich has developed a way of helping its employees to deliver quality consistently to customers and has called it iQUALITY. This acronym is designed to help define what quality looks like at Zurich. It reminds staff that quality is a key part of every interaction they have with customers.
Zurich recognises that quality is not a ‘one-off’ process. Its commitment to providing a world-class service requires that it continuously listens to its customers’ changing needs and expectations. It puts in place the appropriate processes and people to meet these needs. Employees play a crucial role in delivering quality service. Zurich encourages its staff to:
- ‘see…the benefits of getting things right, first time, every time
- hear…what our customers want, keep our promises and deliver
- feel…empowered and add value to the business and the customer experience
- think…about how customers perceive Zurich.’
Managing quality
Quality control
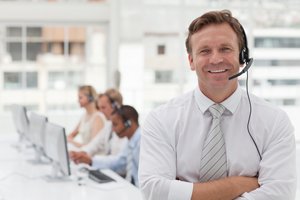
Quality can be managed in several ways. It can be measured at the end of a process to make sure that any sub-standard products do not reach customers. This is known as quality control (QC).
This procedure is most often used in product manufacturing. The process involves testing a sample of the product as it comes off the production line. Putting things right at the end of a process is often costly. In a manufacturing environment, extra items must be made to replace the faulty products. There will also be costs in terms of the staff time needed to put things right and other resources. For example, it may not be possible to recover or reuse the materials from faulty products.
In a service industry, a quality control approach is rarely enough to maintain standards. This is because many aspects of a service are only realised as they are delivered to customers. For example, an insurance company can only deal with a claim on a policy when the customer makes a claim. This is why many businesses use other ways of managing quality.
Quality assurance
One approach is quality assurance (QA). Quality is not simply considered at the end of a process but at every stage. Processes or procedures can be measured against set standards or ‘best practice’ benchmarks within the industry.
TQM
Total quality management (TQM) is an approach that seeks to ensure that all parts of a process are ‘right first time’. The aim is for ‘zero defects’. A TQM approach requires every employee to take responsibility for delivering quality. TQM looks at improving both the people and processes involved in the business through continuous improvement.
iQUALITY
Zurich’s approach to managing quality uses a combination of the methods above. Firstly, it uses iQUALITY to embody the principles of TQM, helping to bring this to life in the minds of its employees so they apply it to the customer care experience every day. Secondly, Zurich carries out regular quality sampling of the customer care it provides and the outputs it produces, e.g. letters and benefit statements. The amount of quality sampling carried out depends on the level of the employee’s experience and the complexity of the task. For example, work produced by a new recruit may initially be subject to QA whereas, for an experienced employee, quality sampling will normally be carried out as a percentage of the work they complete. If the quality sampling for the experienced employee identifies a trend of errors, the percentage of quality sampling may be increased.
‘Five whys’
In practice, it is difficult to remove errors completely from a business process. To drive continuous improvement, what an organisation can do is identify errors and put them right. Zurich uses a process known as ‘root cause analysis’. This is a way to find out why something went wrong and to find ways to stop it from happening again. Zurich applies the ‘five whys’ approach to root cause analysis. Staff involved in quality management look at the ‘trigger’ that brings attention to the problem and then repeatedly ask ‘why’, probing deeper, until the true root cause is discovered. Once this is identified, Zurich can devise a suitable solution to stop it happening again and then monitor outcomes to make sure that the solution is addressing the problem.
For example, one issue facing Zurich was that it was receiving a number of similar complaints from customers about not receiving payments promptly when their savings policies matured (came to an end). The complaints were the ‘trigger’ in this case.
Using the ‘five whys’ approach, Zurich found the root cause was that the manual process for issuing claim packs and sending payments for these policies was causing delays. Zurich changed the process so that packs are now sent out earlier and the payments are sent out automatically 10 days before a policy matures. This ensures customers receive payment promptly. There has since been a 78% fall in complaints related to this issue.
Measuring quality
In order to measure quality, a business needs to establish key measures to track how well it is meeting standards. It could, for example, measure how many customers buy other products from the company (repeat business) or how fast it responds to customer queries (customer response rates). Zurich’s UK Life business deals with over half a million calls, emails and letters a month. Just 0.3% of these are complaints. Zurich is quick to respond to any complaints or issues raised by its customers.
It is also important for a business to capture and regularly review the results of its quality management processes against its own or industry-set benchmark standards. This can help to identify problem areas and enable preventative steps to be taken to correct the problem or prevent it from getting worse. Unidentified problems may lead to inferior service which, in turn, could reduce customer satisfaction. Zurich uses a quality framework to regularly review the results of its quality measurements against benchmark standards.
A business may also use measures set by outside bodies such the British Standards Institute (BSI) or against the performance of other businesses in its industry. As a provider of financial services, in the UK Zurich is regulated by the Financial Services Authority (FSA). This sets out rules and regulations covering all aspects of the business, including the concept of Treating Customers Fairly.
Zurich measures

Zurich’s approach to customer centricity aims to go beyond the requirements and standards set out by the FSA and BSI. As a global business, Zurich aims to be the best insurer as measured by all its main stakeholder groups – its customers, its shareholders and its employees.
For a customer-focused business, levels of customer satisfaction are one of the most important measures. Zurich aims to be in the top 25% of insurance providers for customer satisfaction. High customer satisfaction scores should be reflected in repeat business and growth in sales. Zurich conducts extensive market research with large numbers of customers. They help managers to understand how far the company is meeting customer needs. Zurich also uses an independent measure called the TRI*M index. This assesses how well different parts of the business are satisfying customer requirements.
As part of its customer impact scheme, Zurich asks customers to rate the company’s performance. Most recent results show that most customers rate Zurich as good, very good or excellent in the three key areas aligned to its business objectives.
Industry awards
Another measure of how well a business is delivering on its promises are awards from within its own industry. Recent awards for Zurich include two Five Star Service Awards at the FT Financial Adviser Awards. This followed an intensive voting process involving 25,000 questionnaires – the biggest poll in the financial services industry. Zurich also received an Outstanding Achievement Award at the FT Adviser Online Service Awards 2011 in recognition of the way that it has maintained a level of excellence since the awards began five years ago.
Benefits of managing quality
There are costs involved in setting up systems to manage and improve quality. It requires staff to spend time in training or in monitoring processes. It requires investment in quality measurement systems.
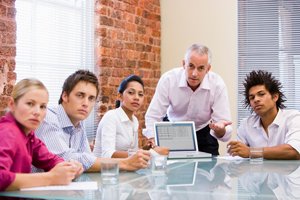
The costs of running large-scale customer surveys are significant both in time and money. However, direct feedback is essential in order that a business understands what its customers think about its service and, importantly, what it can do next to increase their loyalty. A quality-conscious business recognises that these costs are a good investment and that the benefits of managing quality outweigh these costs.
Providing quality services delivers benefits to the business. It can gain savings from having more efficient staff and processes, higher productivity and fewer rework costs. Some benefits are harder to measure but also add value within the business, such as improved staff morale and motivation. These help to retain staff, build experience within the business and save on recruitment costs.
Good quality should also be reflected in the bottom line – in sales and profits. In many service industries, the quality of service is the key factor that helps a business to outperform its rivals. High levels of customer care create high levels of customer satisfaction which can give the business a competitive advantage.
In the Financial Services industry, products and prices can appear very similar to customers so customer care is the differentiating factor between providers. Customers that have a positive experience are much more likely to renew their policies, buy other products and services and recommend the company to others. Not managing quality could lead to disappointed customers, who could easily choose to take their business elsewhere. Zurich’s customer care sets it apart from others in the industry, maximising potential to retain its customers.
Conclusion
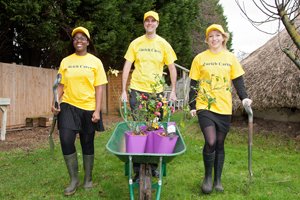
A quality product or service is one that does what it is supposed to do – that is, meet customer requirements for its target market. For a business, therefore, quality is based on knowing what customers need and expect and meeting these demands.
A business that is serious about quality does more. Zurich aims not only to meet customer expectations, but also to exceed them. Zurich puts quality at the centre of how it does business. It actively manages and measures the quality of the service it provides to make sure its customers receive the best possible level of customer care.
Zurich | Creating quality customer care