A quality material, product, process, service or system is one that meets the needs of customers. Today, customers, including consumers, know what they want and can easily recognise ‘quality’.
Businesses interact with a variety of customers e.g.
- Internal e.g. staff who have their office cleaned, or use the canteen
- Business e.g. suppliers of raw materials, stationery, transport, telecommunications
- End users e.g. other firms, the government or its agents, or the general public (buyers of goods or services).
Many businesses trade at local, national and international levels. To win customers’ confidence, firms need to meet the highest quality standards. Distant and local or national customers want a guarantee of reliable, high quality goods and services.
The British Standards Institution (BSI) provides a range of products and services that assist in assuring high quality. It was the world’s first national standards body and is the best known worldwide (as indicated by its official ‘Superbrand’ status).

There are approximately 20,000 current standards that all capture best practice. They are established by 1,113 different committees of specialist experts who reach a consensus about what should be expected of a particular product, material, service, process or technology in a particular industry – e.g. the structure of a gas pipe, the design of an electrical wiring system. Committee members have a wide range of interests and skills from manufacturers, sellers, research organizations and government departments to campaigners, users and consumers. The standards produced are regularly reviewed to meet the changing demands of society and technology.
BSI’s development
Today, the majority of UK output has moved to services. So, in addition to providing standards for products and materials, BSI creates standards for services and systems, including management systems. It leads the development of standards for many important new areas of business activity. These include:
- improvement of utility billing services (e.g. gas and electricity suppliers)
- products being developed with new technologies e.g. nano technology (the creation of miniature products and processes)
- implementation of web design processes, to ensure characteristics like usability and readability.
BSI is a global group of companies, offering a wide range of standards-related services including certification and product testing.

The ‘British Standards’ division – the part that creates the standards – also serves as the UK’s National Standards Body. Some of its funds come from the government for promoting and protecting UK interests worldwide, as well as helping British businesses to be innovative and competitive.
The rest comes from commercial activities e.g. selling standards to a wide range of companies including SMEs, providing advice and training and selling books/guides explaining how to meet and get the most from using standards.
The rest comes from commercial activities e.g. selling standards to a wide range of companies including SMEs, providing advice and training and selling books/guides explaining how to meet and get the most from using standards.
Why are standards needed?
At a personal level we can see why standards are important. They provide a guarantee of safety, predictability and usability. We do not have to worry whether our electrical wiring is safe or that a piece of paper will fit into an envelope and we can play any CD in any machine.
Standards provide a safety net for many areas including clothing, food, furniture, transport and air quality. They remove anxiety for consumers by assuring the fitness for purpose of items we buy and use, as well as creating confidence in the businesses we are buying from.
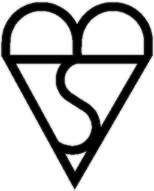
BSI’s ‘Kitemark’ is a quality assurance mark appearing on a wide variety of traditional and new goods. It is a form of guarantee that a product is made to a quality standard. It can be found on a range of well known products tested by BSI to make sure they meet the relevant standards e.g. crash helmets, refrigerators, electrical plugs, Christmas tree lights.
As consumers we want standards because they:
- inform us about the reliability and fitness for purpose of the goods and services we buy and use
- enable us to use more things more widely giving us greater choice
- bring peace of mind.
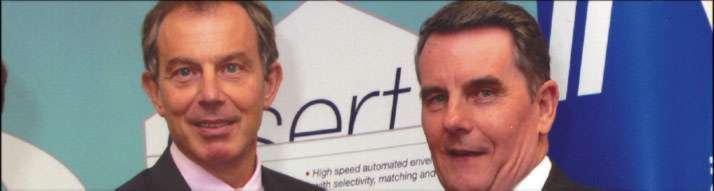
Manufacturers and retailers welcome standards, because they:
- provide clear guidelines on targets that reflect best practice
- protect manufacturers against poorer rivals who might otherwise damage an industry’s reputation
- provide an excellent selling point
- provide a benchmark that can be used for communicating the specification and characteristics of the product, process or system, and from which improvement/innovation can be easily explained
- provide competitive advantage by making it easier, cheaper and more efficient to produce and sell things in the UK and internationally.
Today there is a range of internationally developed standards: European Standards (ENs) created for operations within the European Union and International Standards (ISOs) which can be used worldwide.
Implementing a quality system
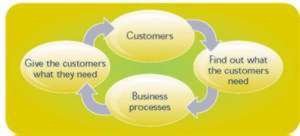
The most successful modern companies manage to identify their customers’ needs and create the processes that enable the business to deliver them.
One most important aspect of BSI’s work is helping organizations to develop management systems which meet the ISO 9001 standard. This involves setting up systems to ensure that processes are customer focused. It also requires a company to improve its quality management system continually.
From 2004, companies wishing to be registered for the certificate must conform to the latest version of the standard ISO 9001:2000 Quality Management Systems Requirements.

It is attention to customers’ needs that drives the system.
- The starting point is discovering what customers want through market research.
- The most important end result is customer-focused products or services. Market research determines what to produce and how. Checking on customer satisfaction measures how effective the quality system is.
- Managers have a responsibility to discover what customers want and to satisfy their needs. To deliver, they manage the organization’s resources, including people (human resources), machinery and raw materials.
- By measuring and reviewing results continually, the organization’s performance improves continuously.
To implement a quality management system, an organization will need to:
- identify the processes that will make up the quality management system i.e. carrying out market research to identify customer needs, conducting a customer satisfaction survey to monitor the existing service
- determine the sequence and relationship between these processes
- identify methods to ensure these processes are carried out well
- make resources and information available to run these systems well
- measure and record how well systems run
- carry out actions needed to achieve planned results, and to ensure continual improvement.
To achieve ISO 9001:2000 a company must show that top managers are committed to the quality system and regularly communicate with all of the organization’s members about the system’s importance.A vital part of developing the quality management system is to plan and deliver training about quality issues throughout the organization.
The company must also register with a registrar (a body like BSI) who visits and assesses the company’s quality management system (QMS) and, if satisfied, issues an appropriate certificate. Follow up visits are carried out to ensure the processes in place are continually revised and improved.
Implementing quality management systems: case studies
BSI’s work in supporting the implementation of quality management systems is best illustrated through company examples.
Forticrete
Forticrete is a leading UK manufacturer of masonry, walling, cast stone and innovative roofing products. It employs almost 500 people across 11 manufacturing sites, supplying products to both the public sector (including health and education clients) and private sector clients (housing and commercial). The company has implemented quality systems for a number of years and made the transition to ISO 9001:2000 in late 2001.
Through implementing the new standard, Forticrete made some key changes to its existing systems. These included:
- attempting to become a paperless office – Forticrete’s paper based system required eight manuals, but the new system is an intranet based flowchart format
- placing more focus on the customer at the centre of the system.
The positive results of developing ISO 9001:2000, as shown by a recent Customer Satisfaction Survey are:
- a 18% improvement in product quality
- a 18% improvement in customer satisfaction ratings
- a 21% rise in performance against competitors
- a 42% reduction in product complaints.
BSI worked closely with Forticrete, identifying ways of making improvements. These included introducing:
- a company newsletter
- an intranet and appraisal system to improve employee communication and training.
The new appraisal system enables employees to identify their individual needs, which the company then works to meet. Employees who are happy and fulfilled are far more likely to help the company deliver customer satisfaction.
Achieving ISO 9001:2000 has helped Forticrete to win a number of national awards, including the Queens Award for Enterprise and, in 2004, the Building Construction Best Practice Award.
British Gas

British Gas is the UK’s leading installer of domestic gas central heating systems. The company provides home energy related services covering gas, electricity, water and home security and is part of the Centrica Group, which also owns One.Tel. British Gas was the first company to achieve a Kitemark for a service.
The company wanted to achieve ISO 9001 for one key reason, it was keen to operate common processes and procedures across such a diverse company. British Gas not only offers home energy services (through British Gas Services) but also plumbing and drains care to customers (through Dyno Rod).
The benefits resulting from implementation of ISO 9001:2000 include:
- employee support for the initiatives, with clearer work targets
- improved relationships with suppliers
- cost savings resulting from improved processing of contracts, reductions in unnecessary rework, reductions in duplicated visits.
The improvements helped the company to achieve external recognition, e.g. winning the Queen’s Award for Enterprise and the Royal Warrant for Services to the Royal Household and the attainment of corporate recognition to the Investors in People standard.
BSI helped the company by identifying areas for improvement and providing ongoing advice and support. This enabled the company to improve in several areas of service provision. British Gas’ Managing Director supports the quality management system, which is integrated across the whole company.
As with Forticrete, following certification to ISO 9001:2000, British Gas is now developing electronic systems to replace and complement existing manual ones. Typical examples of documents that had to be produced included:
- a quality policy
- a list of quality objectives
- a quality manual
- other planning documents.
The benefits of developing a quality management system
Working with BSI, companies are able to reap many benefits from achieving ISO 9001 certification and other standards (e.g. standards for the development of Environmental Management Systems – ISO 14001, and Information Security Management Systems – BS 7799).
These include:
- achieving greater levels of customer satisfaction
- meeting legal requirements
- winning the trust of suppliers and customers
- improving the management of a company by meeting management standards
- reducing costs and making better use of time
- building a reputation for integrity.
These all enable company’s to build superior, more prestigious brands. Additionally, companies are able to strengthen their international reputation, thus building up their export business.
Conclusion

BSI was the world’s first national standards making body. Today it is the most prestigious international standards institution.
It works with the British government, manufacturers and other stakeholders to create quality standards. These guarantee fitness for purpose, and help British manufacturers to gain a competitive edge both in the UK and internationally.
BSI assists British businesses in all markets to grow and to concentrate on meeting customers’ requirements.