Imagine a world in which consumers cannot tell how reliable a product or service is and have no knowledge about the suitability of things they buy and use. It would be dangerous and chaotic. The creation of standards with which products and services comply helps eliminate such chaos and enhances consumer welfare, satisfaction and safety.
In the UK, the creation of standards is the responsibility of the British Standards Institution (BSI), the UK’s National Standards Body. BSI Group has a £232 million turnover and employs over 5,500 staff in more than 100 countries. The BSI Group:
- Facilitates the creation of standards and promotes their use
- Tests and certifies products
- Assesses management systems
- Inspects commodities.
The British Standards division, based in London, has established over 20,000 standards and is actively involved in developing European and International standards that meet global needs and those of businesses in the UK, many of whom operate worldwide.
BSI was the world’s first National Standards Body and is exceptionally well qualified to play a global role. Its most widely recognised mark is the Kitemark:
Research shows that 80 per cent of British adults recognise the Kitemark and 60 per cent are prepared to pay a higher price for products that carry it, for the reassurance it gives. Products that carry the Kitemark have been tested against British Standards and organizations are only able to obtain and display the Kitemark after thorough and regular independent product testing and quality management systems assessment.
Standardization and quality

Standardization is vital in creating and sustaining quality. Quality is the extent to which a user’s needs and expectations are met. To protect consumers, establishing ‘fitness for purpose’ is crucial for many products e.g. a medical dressing, a car tyre.
A level of quality is achieved by an organization’s compliance with an acceptable standard for the product, and also compliance with another standard for the organization’s effective quality management system that ensures consistent achievement throughout its production processes.
Standards are applied to many materials (e.g. paint), products (e.g. hair dryers), methods (e.g. wiring a house), and services (e.g. travel information). They simplify aspects of our lives and increase the reliability and the effectiveness of the goods and services we use.
We all rely on one another in a global economy so standards provide peace of mind that products will work together, no matter what their origin. For example, credit card standards benefit:
- Credit card users who know their cards will work
- Credit card issuers who know their own and their customers’ needs will be met
- Credit card manufacturers who know what size and specification to manufacture to
- Automated Teller Machine (ATM) manufacturers who know which data needs to be read.
Standards

We live in a global market place in which common standards are becoming increasingly vital e.g. fire safety standards for new buildings, and limits on pollutants in the interests of environmental protection and public health.
From a UK perspective, membership of the EU is important too, as are our trading links worldwide. As a result, stakeholders in the UK are interested not only in British Standards but also in European Standards and International Standards, and BSI helps to serve the UK interest in their creation.
There are a variety of ways of developing standards. The time they take to create depends on their intended use and the number of different groups needed to reach consensus.
Standards that involve representation from business, government and society are known as formal standards and may take two years or more to create. A number of other standards are also often created, such as codes of practice, and guides to the use of standards for particular types of business or industry.
Benefits to stakeholders
Standards relate both to products (how particular products function or interact, e.g. electrical plugs, or how services are delivered e.g. crowd control) and to management systems (e.g. how environmental protection systems will be overseen and managed). Everyone benefits from standard setting and their benefits are inter-related.
Businesses are key beneficiaries, because standards create clarity and certainty and remove confusion. Meeting the required standard gives an important marketing advantage – firms able to state that their products meet BSI standards are more attractive to customers.
Standardization is beneficial because it:
- Helps businesses to be commercially viable. Producing standard products, or products assembled from standard parts, makes sense to manufacturers and service providers because standardized products and parts reduce design, production, warehousing and distribution costs.
- Is reassuring. Because when goods conform to certain standards in order to be put on sale, consumers know they can believe the claims that producers make for them.
- Is protective. The standardization process gives a high priority to health and safety. Standardization assures safety, offers consumers assurance, and helps to create a cleaner environment (through environmental standards).
- Helps businesses to be cost effective and time efficient. Creating a standard is relatively straightforward because BSI has tried and tested processes for doing it.
An important aspect of standardization that makes it attractive and acceptable to business is that it is market led – the standards set meet customers’ needs.
For example, building contractors require electrical fittings that meet British Standards in order to offer guarantees to those people who have contracted the builders’ services. House buyers also know that fittings and components are made to standards and are safe to use and offer greater security (for example double glazed windows and door locks). Some of these standards are required by law.
Formal standards also promote fair competition and avoid the abuse of economic power by creating an open market, based on standards that have been developed with a wide consensus.
The Government’s need to regulate business activity directly is reduced because standardization is a form of self-regulation. Importantly, under European law, standards may be used by manufacturers as a way of demonstrating compliance to European legislation.
Creating new standards is an ongoing process. This is illustrated by the recent European Union Directives on Waste Electrical and Electronic Equipment (WEEE) and the Restriction of the Use of Certain Hazardous Substances (RoHS). These are designed to reduce the adverse impact of obsolete electrical equipment (e.g. computers, refrigerators) on the environment at the time of disposal.
The Directive makes manufacturers financially responsible for the reuse, recycling and recovery of WEEE. It becomes enforceable by August 2004. Responding to this directive in the UK involves relevant manufacturers working with technical experts and BSI to create new manufacturing standards and systems that will help to dramatically reduce such wastes (which currently account for 4 per cent of municipal waste in the EU) to the benefit of consumers. BSI thus continually works with stakeholders to create better standards.
Standardization of quality management in the supply chain
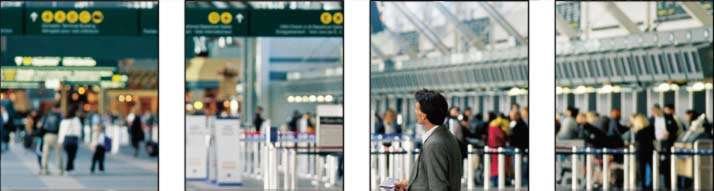
In the developed countries of the modern world the emphasis is on some form of quality management. The implementation of business excellence models, total quality management or ISO 9001 quality management systems is almost taken for granted and has long since improved on the original idea of quality control, which involved inspectors checking finished goods and rejecting those that did not meet the required standard.
Modern quality management systems encourage everyone in the workplace to think about quality in everything they do. Every employee is encouraged to think in terms of final consumers and place them at the heart of the production process.
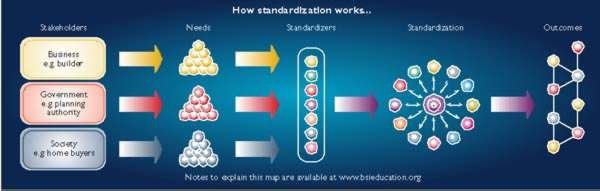
When a firm is certified to International Standard ISO 9001, the certificate indicates to potential customers that the organization has continual improvement processes in place for the specific purpose of enhancing customer satisfaction. From this, consumers can reasonably infer that such businesses are able to deliver the promised quality product or service consistently.
Continual improvement of the quality management system involves:
Managing by systems and operating through processes
- Identifying current and future customer requirements and meeting them
- Continually improving management systems: measuring, monitoring, analyzing and improving.
BSI supports the application of quality management systems and standardization throughout the supply chain. This can be achieved by designing and implementing a single quality management system that can apply to product or service standards for all activities within a business. The single management system can also incorporate other management systems standards that contribute to sustainable development and corporate social responsibility.
Management systems can be applied to quality, environment, risk, information security, and health and safety. For example, the Environmental Management System standard, ISO 14001, helps organizations to manage their environmental impact, such as the control of waste and pollution activities, at every stage of production.
The management systems can be used in any combination as one system, or can stand alone. The audit system, leading to certification, can be applied to a combined system, or to one. Each standard has a common structure based on: plan, do, check, act.
Standardization and safety
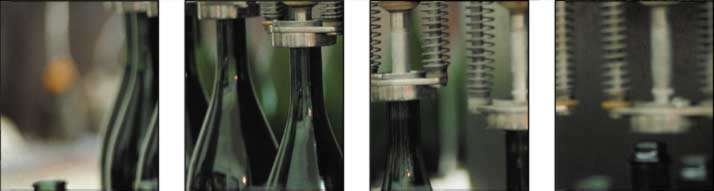
Consumer safety features strongly in the setting of standards. For example, with UK wine consumption rising, opening wine bottles safely has become a higher priority. Recently, the British Glass Manufacturers Confederation (BGMC) helped to create a set of guidelines for the design of a cork removal device for wine bottles so that the operation can be carried out safely.
There are several standards for the manufacture of different glass bottles, for example for carbonated soft drinks, and compliance with them enables production consistency in the glass industry. This also helps British glass manufacturers to meet safety standards that retailers are looking for.
Today, UK legislation requires manufacturers to comply with European Union Directives, and standards are a good way of doing this. A good example is of the Directive for electrical equipment that relates to safety standards for household equipment such as televisions, DVD players and vacuum cleaners.
Again, and happily for even the most inquisitive DIY person, modern standards require that consumers cannot easily reach the parts of domestic products that involve high voltages so that electrocution risks are minimised.
BSI’s stakeholder approach means that consumers’ views have high priority. When, for example, consumers complained that the outside of some toasters became dangerously hot, new standards of heat insulation were introduced.
Conclusion
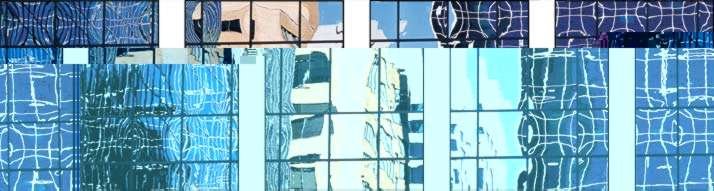
BSI has a vital role. Establishing clear standards creates order in an increasingly complex world. Standards meet changing market needs and are customer driven.
Businesses benefit from standards because they establish ground rules that help to guarantee quality. Achieving certification to a standard might add reassurance for its customers and enables a business to boost its sales performance.
Consumers benefit because their safety and their satisfaction are both greatly enhanced. Governments benefit because such measures contribute to greater productivity and economic growth, and safer work, leisure and home environments. BSI | Standardization and quality management